Philipp Pruesse, Sales Manager, Dimensionics Density
In the ever-evolving world of manufacturing, Additive Manufacturing (AM) has emerged as a ground-breaking technology with transformative potential. From aerospace to healthcare, AM has revolutionized industries by enabling the creation of complex, customized parts with unprecedented precision. However, beneath the surface of these intricate 3D-printed objects lies a critical aspect that often goes unnoticed: density. The density of AM parts plays a pivotal role in determining their material properties, structural integrity, and overall performance. In this article, we will delve deep into the significance of density determination in AM, exploring how it assesses the quality of metal 3D printed parts and the impact it has on various industries.
UNDERSTANDING THE BASICS: WHAT IS DENSITY DETERMINATION?
Density determination in AM refers to the measurement and assessment of the material’s density within a 3D-printed object. It is a key quality control parameter that helps manufacturers ensure that their printed parts meet the desired specifications and standards. In essence, density determination involves evaluating how closely the actual material density of the 3D-printed part matches the intended or theoretical density.
Density determination presents a unique challenge due to the layer-by-layer deposition process inherent to AM technologies. In AM, parts are built up incrementally through the deposition of material in thin layers. This layering introduces the potential for voids, defects, and inconsistencies that are often hidden within the printed object. Unlike traditional manufacturing processes, where materials are moulded, machined, or cast as a whole, AM relies on additive techniques that make it harder to assess the internal structure of the part during production.
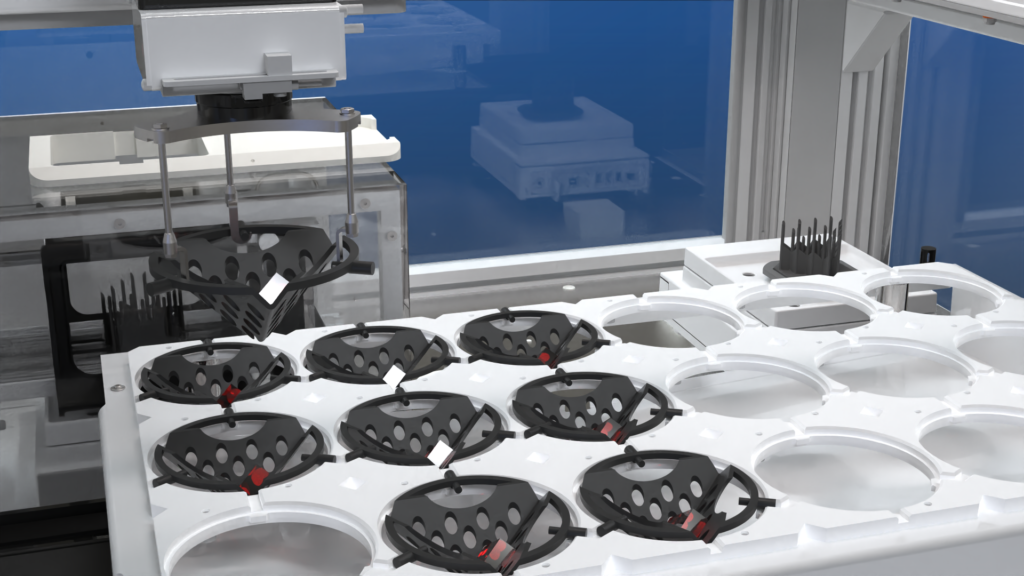
In addition, the sudden and highly intense energy deposition in laser and ebeam processes creates a small area of molten material which then immediately solidifies as the energy source move on. This sudden incoming burst of energy can scatter powder particles across the bed uncontrollably, and if too high (or the material is exposed for too long) can cause some constituents of the alloy to become overheated, leading to gas pores which are unwanted in a solid structure. Similarly, in Metal Binder Jetting (where the powder particles are aggregated by forcefully spraying droplets of binder upon the desired areas) the jetting process can cause the same particle scattering effect in the powder bed.
Consequently, density determination becomes critical in AM to ensure that each layer has fused correctly, that no contamination or gas pores have been created, and the overall part attains the desired material properties, structural integrity, and performance.
THE IMPORTANCE OF DENSITY IN MATERIAL PROPERTIES
Material properties are at the heart of any manufacturing process, and in AM, they are closely linked to density. The density of a 3D-printed part influences several critical material properties, including mechanical strength, thermal conductivity, and electrical conductivity.
Density is directly proportional to the mechanical strength of a material. In metal AM, a high-density part exhibits greater tensile strength, which is crucial for applications in industries such as aerospace and automotive, where structural integrity is non-negotiable. Engineers and designers depend on accurate density determination to ensure that components can withstand the stresses and loads they will encounter during operation.
The density of a material also affects its thermal conductivity. Components with optimized thermal conductivity properties are essential in heat-sensitive applications. Accurate density assessment allows for the production of parts with superior thermal performance, making them suitable for use in electronic devices, heat exchangers, and more.
In industries like electronics and telecommunications, electrical conductivity is paramount. Density determination ensures that metal 3D printed parts meet precise electrical conductivity requirements, allowing for the production of components that perform reliably in demanding electrical applications.
STRUCTURAL INTEGRITY AND DENSITY
The density of a metal AM part plays a crucial role in determining its structural integrity. Density in metal AM refers to the degree of material consolidation and fusion achieved during the printing process. A high-density metal AM part signifies that the metal particles or layers have effectively bonded together, resulting in a solid and homogeneous structure. This high-density structure is more resistant to crack initiation and propagation, offering improved structural integrity and the ability to withstand mechanical stresses. Conversely, a low-density metal AM part may contain voids, porosity, or incomplete fusion, making it prone to defects and reduced structural integrity, making it less reliable for demanding applications in industries like aerospace, automotive, and healthcare.
The relationship between density and structural integrity is particularly critical in situations where safety, durability, and performance are paramount. High-density metal AM parts are more likely to meet stringent quality and safety standards, ensuring they perform reliably under various loads and environmental conditions. In contrast, low-density parts may exhibit unpredictable failure modes and a diminished ability to bear mechanical loads, compromising their structural integrity. Therefore, meticulous control over the density of metal AM parts is essential to guarantee their overall strength and reliability in real-world applications. In addition to improved resistance to cracking and mechanical stresses, high-density metal AM parts also tend to exhibit more consistent and predictable material properties throughout their structure. This uniformity is crucial for meeting design specifications and ensuring that the parts perform as intended over their lifespan.
Furthermore, the impact of density on structural integrity extends to considerations of fatigue resistance and long-term performance. High-density parts are better equipped to endure cyclic loading and prolonged exposure to harsh environments without succumbing to material degradation. In contrast, low-density parts may experience premature wear and fatigue, leading to a shorter service life and potential safety hazards.
The density of a metal AM part is a fundamental factor that underpins its structural integrity, mechanical properties, and overall performance. Achieving and maintaining high density through precise process control and quality assurance measures is imperative for meeting the rigorous demands of industries where reliability and safety are paramount.
PIONEERING NON-DESTRUCTIVE DENSITY DETERMINATION
From the above it can be seen that the ability to accurately, repeatably, speedily, and cost-effectively determine the density of AM parts is not just critical to ensure part integrity, but is of huge importance in streamlining the AM validation process and therefore cementing AM’s position as a viable and valid manufacturing technology moving forward.
As the perceived importance of density determination in AM continues to grow, innovative solutions have emerged to meet industry demands for accurate and non-destructive density assessment. Dimensionics Density stands at the forefront of this technological advancement, offering cutting-edge density determination technologies that empower manufacturers to achieve optimal part quality and performance.
The need for automated, non-destructive density determination methods were obvious for Dimensionics Density. Automation ensures efficiency and scalability, enabling quick assessments of multiple AM parts within production cycles. Non-destructiveness is essential to avoid compromising the integrity of valuable components, and it allows for real-time quality control. Furthermore, AM often produces complex and intricate geometries, leading to multiple parts with varying shapes and sizes. Hence, a density determination method needs to be versatile enough to handle diverse AM parts rapidly, ensuring consistent quality and reliability across the entire production line.
Until the launch of Dimensionics Density’s automated density determination technology, manufacturers were forced to use alternative solutions such as micrographs, computed tomography (CT), or the manual Archimedes method which exhibit varying degrees of accuracy, resolution, repeatability, and successful defect detection.
Micrographs, although providing some insight into AM specimen porosity, suffer from the drawback of specimen destruction and significant manual labour, increasing both time and cost while relying heavily on expertise. CT, while capable of generating realistic 3D internal porosity images, demands costly expert operators, has limitations in detecting small pores, and requires prohibitively expensive equipment. On the other hand, the manual Archimedes method, while user-friendly and potentially very precise, tends to be less accurate due to susceptibility to changing environmental conditions, balance precision, and experimental procedure accuracy. Reproducibility is challenging, as results are influenced by human factors, including variations in specimen placement on the balance and manual measurement operations that lead to deviations in measurements.
Dimensionics Density’s solution effectively combines the Archimedes density determination method with modern automation technology. Automated part handling eliminates human influence on measurement, as parts are always placed identically onto scales. The scales are designed to be insulated from vibration. In addition, all ambient conditions such as temperature, air pressure, and water temperature, are recorded via climate sensors, and their influence on the measurement result is taken into account directly in the evaluation algorithm when determining the density.
CONCLUSION
In the realm of AM, the power of density determination cannot be underestimated. It is the invisible force that shapes material properties, ensures structural integrity, and elevates performance across industries. From aerospace to healthcare, the accurate assessment of density is instrumental in creating components that meet the highest standards of quality and reliability. As pioneers like Dimensionics Density continue to advance non-destructive density determination technologies, the future of AM promises even greater precision, efficiency, and innovation, pushing the boundaries of what is possible beyond the surface.
Leave a Reply
You must be logged in to post a comment.