Smart Manufacturing, Industry 4.0, Industrial Internet of Things – whatever you call it and wherever you sit in terms of development, implementation and use, machines are processing huge amounts of data to make real-time decisions on their own, often with little or no human interference. For this article we are going to stick with ‘Smart Manufacturing’.
Storing and analysing data is a key requirement for Smart Manufacturing. Machine health, down-time, throughput, to name a few are all types of data that needs to be stored accessed and analysed. The human interface to accessing this information is generally straight forward through a PC or terminal and also having the ability to look at multiple machine data in a custom software application.
In order for data to be valuable, processing has to happen in the appropriate fashion and Smart Manufacturing can enable better competitiveness by changing production processes using high-speed data.
Data challenges
In the smart facility, sensors collect data such as temperature, light and air flow. Devices track production yield, monitor assets, worker safety and many more. Machines generate a lot of content with changing characteristics: some processes require high-speed data whose value will diminish as time passes, and usually comes from a variety of sources, and the constant flow being streamed from sensors and devices are typically unstandardised and unstructured. Considering all these, the big challenge is how to transform “content” into “context” and enable machines to process this constant stream of high-speed data in real- or near-real time, to self-diagnose and learn, and facilitate decisions that will improve processes and/or prevent disruptions.
For many critical operations, latency is a major issue. Any additional wait time can disrupt operations and heavily impact the business. Due to the intense need and demand to accelerate the manufacturing process, storage is shifting from heavy reliance on the cloud to the edge.
Data Challenges: Traditional vs. Smart Factory
Edge computing as applied to smart manufacturing refers to storage and processing capabilities right where data is collected or where certain actions are performed. In contrast to a centralized location (cloud), edge computing is decentralised, as resources and services are distributed among storage computing gateways or servers which serve as intermediaries before data is sent to the cloud. Herein lies the problem. Latency.
Latency is the amount of time it takes a message, or data, to traverse a computer network. High or long latency is slow and fast is low latency. To put this into numbers 100 milliseconds is considered good and 50 or below very good latency. Using a wi-fi network with vast amounts of machines will ultimately have a higher latency. ‘Hardwiring them’ would solve this problem but who wants miles of wires in a Smart Factory. It defeats the object of being Smart.
We are now seeing more automated process collecting data at the edge, or a local device or machine. By shifting from a centralised (cloud) storage to distributed (edge) storage, businesses can realise numerous benefits, such as better equipment uptime, lower maintenance costs, reduced equipment failure, boosted manufacturing and overall enhanced operations. Edge storage is enabling the collection of factory data that will help manufacturers quickly identify the root cause of problems resulting in poor production quality or machine downtime.
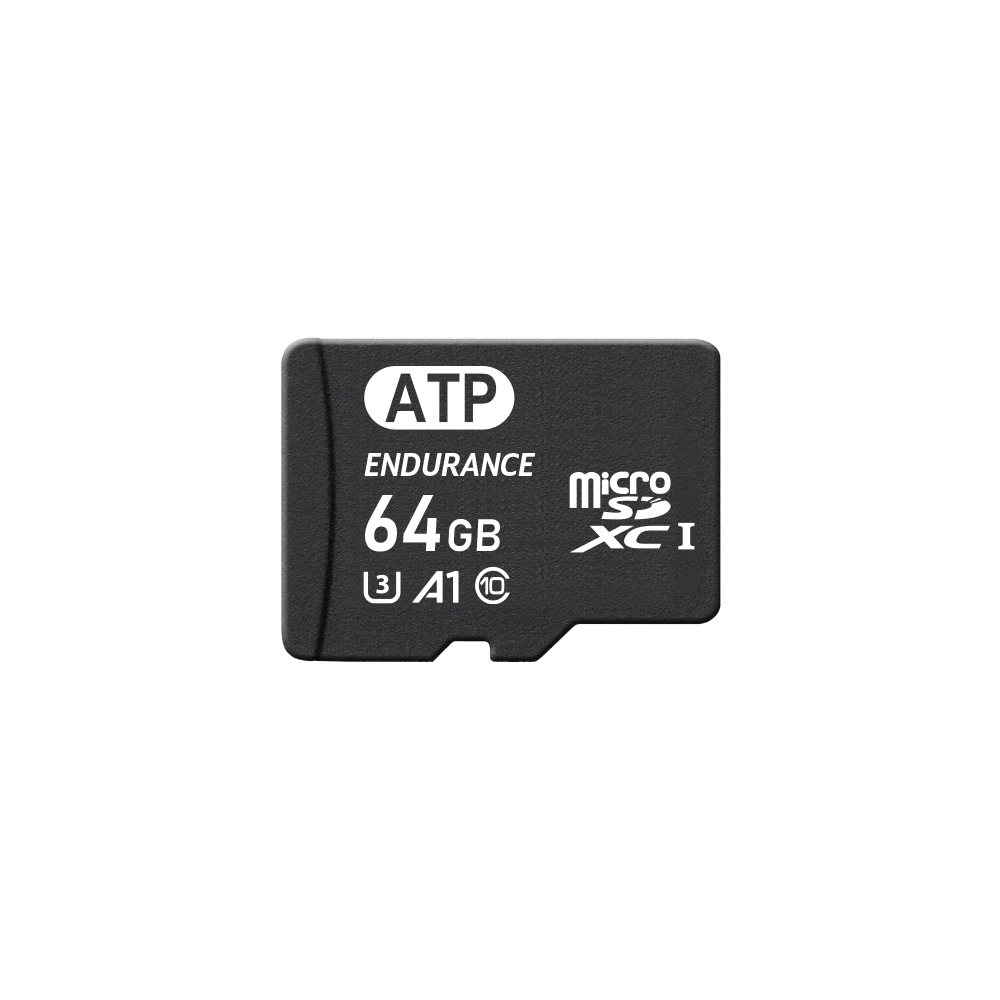
Edge storage.
What does that mean? Edge storage is data that is collected and stored within a device or a machine. This could mean an internal SSD, or even something as small as an SD or microSD card. We are not talking Commercial grade storage. Industrial storage is for industrial devices and there is a wealth of differences between the two.
Next generation of memory cards
Endurance in mid-capacity (8-64GB) memory cards has always been the Achilles heel for this kind of storage, which is largely down to the type of NAND Flash (or memory chip) being used within the card. Until now.
ATP Electronics is the first company to have developed a high-capacity memory card capable of over 109K hours of continuous recording with a whopping 3,840TBW endurance in pSLC mode utilising industrial grade 3D TLC NAND Flash. All this at a price point which sits comfortably between purchasing and engineering requirements. The S750 SD and microSD cards are available in both commercial and industrial operating temperatures and offer a whole host of customisation options. These low latency cards are perfectly suited for write intensive smart manufacturing equipment and can also be used in surveillance, automotive, autonomous vehicles and DVR applications.
You can get your hands on a free sample of the memory cards by clicking here. Our memory experts can help you get the right fit, form and function for your application.