– Are hang-ups in materials causing production problems?-
Powders, granules, lumps, particulates, bulk solids – call them what you will. Such materials are present in almost all manufactured goods, from cement and gypsum in making plaster to resin pellets and pigments in plastics, to sugar and flour in foods and most of the ingredients and intermediates in pharmaceuticals. They are weighed out, blended, blown through pipelines, dispensed into bottles and bags, compacted into tablets and used in many other circumstances. Yet in spite of the commonplace usage of powder materials, the numerous systems that have to handle them, and the number of operators, maintainers, engineers and managers that have to deal with these systems, there is precious little information in the public domain about their behaviour and about how to select or design systems to work reliably and accurately with them.
Systems handling powders and bulk solids materials often under-perform very badly. The Rand report highlighted 40 new process plants, 20 based on liquids feedstocks and intermediates, 20 using powders and bulk solids; whilst the liquids plants were mostly up and running within 10% of time and budget, the performance of solids based plants ranged from at best poor, to at worst catastrophic! Average cost over-runs were OVER 100% (compared with the estimate against which the case for investment was made); over 60% of the solids process plants didn’t perform to full expectation even 2 years after start-up. Many people are surprised to find there is a branch of engineering that deals specifically with these problems; Bulk Solids Handling Technology. As much an art as a science, sadly it is hardly taught on any BTEC, degree or higher course but once new engineers arrive in industry, many have to grapple with these materials and the difficult problems they bring. Hardly surprising, then, that losses are so severe when dealing with powders.
When the report’s authors looked at the reasons behind this poor performance of solids processing plants, it was invariably lack of reliable flow of the solids between process steps – storage vessels, conveyors etc. In days gone by, when silos, feeders mixers etc were manually controlled, there were people around to clear hang-ups, hammering hoppers or clearing material by hand. However, with more plant automation and de-manning, such material hang-ups cause serious production loss, recipe variation, cross- contamination and other quality and output problems.
Never has it been more important to make sure that plant designers, maintainers, managers and also people procuring process plants, understand the need for careful selection of solids handling equipment. The key lies in understanding the properties of the powder being handled; this requires study, because powders all behave differently, but the first stage is to get people educated in the area so they are aware of the challenges. Short courses are run by The Wolfson Centre for Bulk Solids Handling Technology at the University of Greenwich, and also by the trade body the Solids Handling and Processing Association. With more knowledge, staff can be aware of the issues and take steps to avoid those ruinous cost over-runs and performance shortfalls that this processing area is known for.
By Prof Mike Bradley,
Director, The Wolfson Centre for Bulk Solids Handling Technology
Chairman, the Solids Handling and Processing Association
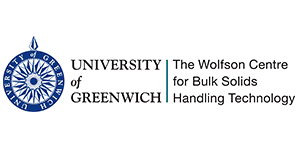
Telephone: +44 (0) 20 8331 8646
Email: [email protected]