Last year the polymer industry experienced complex material supply conditions. Although most British processors were anticipating some turbulence at the end of the Brexit transition period, the added global challenges of raw materials sourcing and price hikes amplified by the pandemic, created the perfect pricing storm.
Jo Davis, Managing Director of British technical moulder Broanmain Plastics summarises the impact of these countless procurement challenges and how their firm continues to navigate the ongoing pricing instabilities.
Severe shortages of raw materials has threatened the survival of SME plastic manufacturers and OEMS across Europe. No production plant has been immune to the effects. “Absorbing rising prices as they reached a six year high while simultaneously overcoming the technical hurdles without compromising production quality has been immensely challenging,” explains Jo.
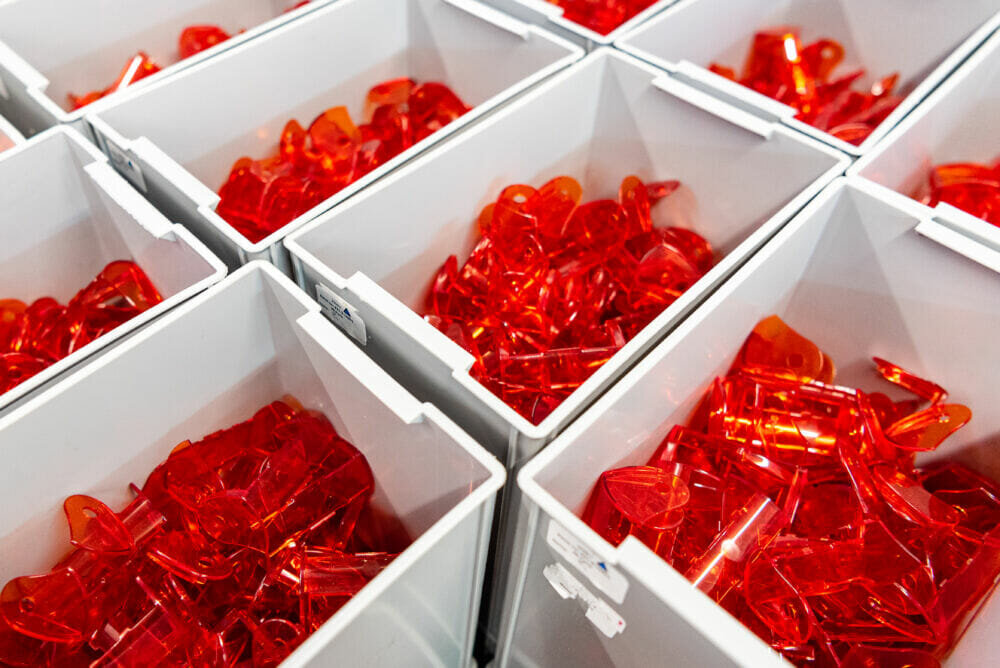
As with many supply chains, there’s several months of lag before higher prices and supply bottlenecks really start to bite. The ripple effects of COVID-19, rising energy costs, plant shut downs, U.S. winter storms, the Suez Canal blockage, suppliers declaring force majeure, and countless other logistical problems continue to leave lingering PE production and supply chain volatility issues.
Given that raw material costs account for approximately 60 per cent of a finished product cost, increasing spot raw material by 150 per cent will naturally push the finished product cost up by 90 per cent.
The tipping point for most processors and their customers came during the 2021 periodic negotiations of future material contracts. Although analysts were optimistic that the issues might be resolved in early 2022, the fallout of price increases and materials shortages still plagues most European injection moulding firms.
As of December 2021, Plastics Information Europe reported little price movement amid weak demand. Simultaneously, compound prices have soared. These can be attributed to the increased cost of titanium dioxide, flame retardants, stabilisers and other additives used widely by technical moulders like Broanmain.
The current situation has highlighted structural flaws. Yet, as an SME manufacturer of technical plastic components, it really demonstrates to us the importance of building out better supply chain resilience. Navigating these instabilities requires a paradigm shift towards better value and risk mitigation, claims Jo.
For domestic manufacturing SMEs, creating this better balance and rebuilding the equilibrium is very dependent on all parties working collaboratively together. To help offset these trade imbalances, Broanmain has put its energy into maintaining longer-term partnerships with trusted material suppliers.
The company is also continuing to invest in technology that increases its production agility and supports its sustainability missive.
“Our most recent IntElect investment helps to ensure that valuable material is not wasted. By targeting zero defects, we can help to ensure that every single pellet is treated with respect and moulded into a high quality part,” emphasises Jo.