By Matt Hale, International Sales & Marketing Director, HRS Heat Exchangers
The concept of Lean production, as developed by Japanese motor manufacturers such as Toyota, is now well established across a range of industries around the globe as a way of maximising efficiency across production processes. What is sometimes less understood is the concept of waste within this model, and how it can be adapted to different situations.
According to the theory of lean manufacturing, anything which does not increase value should be considered as waste or futile effort – known as ‘Muda’ in Japanese. Within this concept, eight different areas which create waste have been identified, which can be summarised with the acronym DOWNTIME:
- Defects
- Overproduction
- Waiting
- Not utilising talent
- Transportation
- Inventory excess
- Motion waste
- Excess processing
The benefits of managing or eliminating the eight wastes include: increased profits due to lower overheads and better utilisation of time and resources; increased customer satisfaction; improved operational performance; and a lower risk business with improved product quality.
Many of these issues will be addressed by good management practices, but there are also areas where the correct choice and design of process equipment, including items such as heat exchangers, processing systems, pumps and fillers, will prevent waste and reduce the factors which contribute to DOWNTIME. Some particular examples of how using the right heat exchanger or thermal system can reduce DOWNTIME are outlined below.
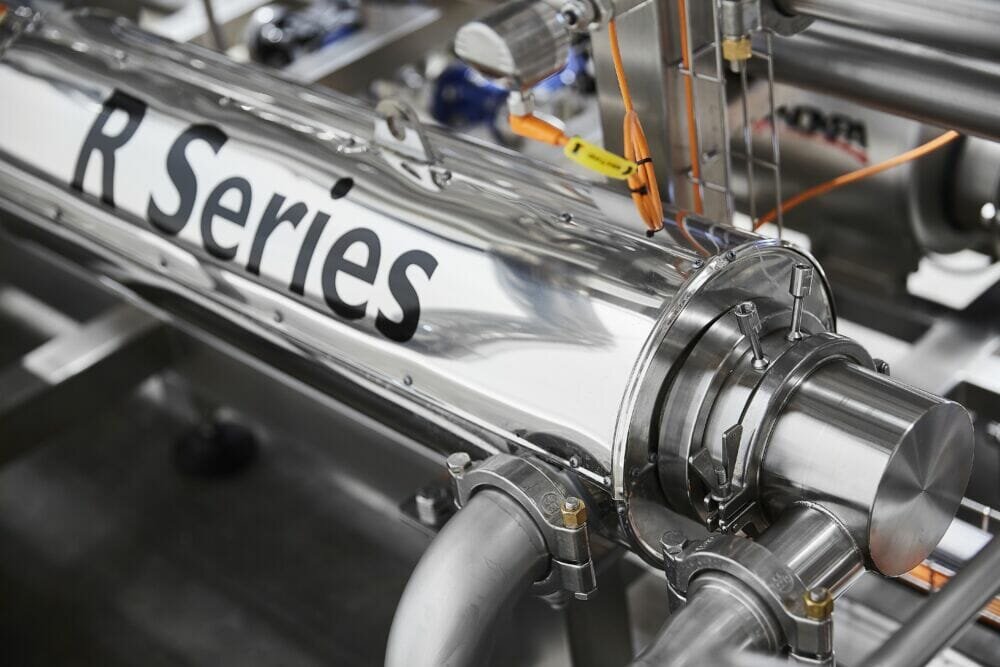
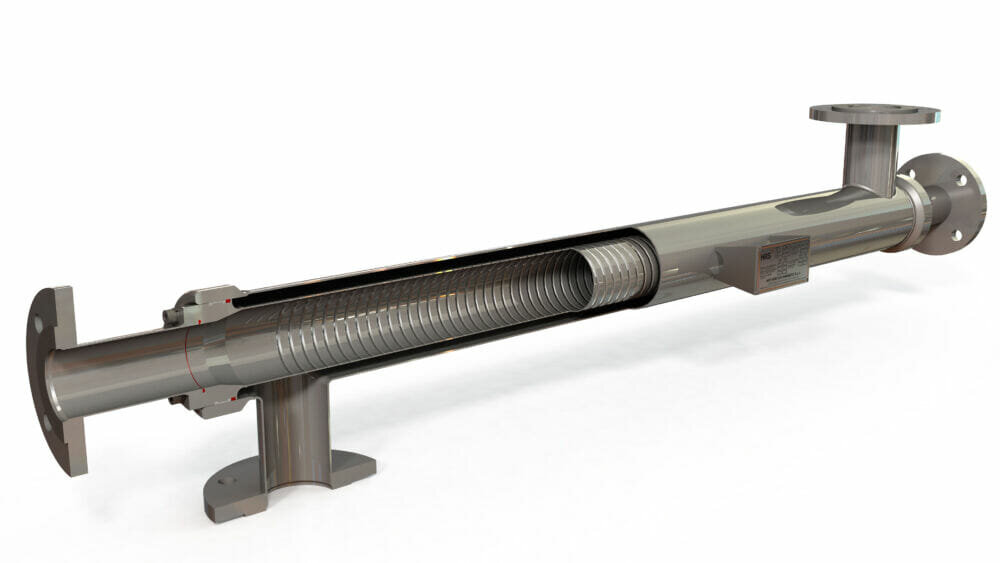
Defects
Defective products which fail inspection or require rework incur the expense of production, but then need additional costs to make them saleable or, in the worst cases scenario, are then unsaleable. One way of ensuring that products meet the necessary specification is to continuously monitor relevant parameters.
The technique works by using an inline instrument to measures changes in the physical or chemical properties of the product, such as concentration. This information is passed to a controller which determines whether to ‘keep’ or ‘discard’ that material based on pre-determined quality parameters.
Such feedback control can be fitted to HRS equipment, and every HRS pasteuriser or steriliser already has a temperature transmitter and a three-way valve to make sure that the set pasteurisation or sterilisation temperature is met.
Overproduction
While most overproduction is likely to be due to manageable issues such as forecasting errors, reducing the amount of product during routine activities such as product change overs and cleaning cycles will also reduce waste and provide savings.
For example, the HRS R Series uses a unique helical screw, which can be used to recover product (either by running through the system or running the helix in reverse). Depending on the product and configuration of the heat exchanger, up to 90% of product can be recovered.
To illustrate the effectiveness of the system, we can imagine a manufacturer of BBQ sauce. Assuming the company makes a profit of 40 pence per litre of sauce, even if 200 litres are lost per production line during cleaning cycles each day, that equates to a loss of £80 a day or £24,000 a year (assuming 300 days production). If the company has four lines, then it is losing almost £100,000 worth of profit, not to mention the creation of around 68 tonnes of waste each year.
Waiting
In the concept of DOWNTIME, waiting extends to areas such as cleaning-in-place, maintenance and reducing general downtime of production lines. Effective product design, such as utilising removable tubes in heat exchangers, can significantly reduce the amount of downtime associated with such tasks, while effective cleaning-in-place (CIP), such as that provided by the stand-alone HRS CIP System, help to reduce downtime due to routine cleaning and product changeovers.
Not utilising talent
Not utilising talent was not actually one of the original principles developed by Toyota but has been added subsequently and is seen as an increasing issue in many businesses around the world. Examples include assigning the wrong staff to the wrong task, poor communication, and a lack of training. While most of these issues will require a management rather than technical solution, the clear design of human-machine interfaces (HMIs) and control panels will go a long way to support clear training procedures.
In addition, the increasing use of remote monitoring and telemetry means that engineers and designers at equipment manufacturers like HRS can be available to help commission and troubleshoot items like heat exchangers and processing systems anywhere in the world. This increases the overall level of knowledge available to on-site engineering staff, reducing downtime and increasing efficiency.
Excess processing
There can be many examples of carrying out multiple versions of the same process, or unnecessary processing in modern businesses, from producing excessive reports or requiring multiple signoffs, to poorly designed processing equipment. One of the strengths of HRS’s corrugated tube technology is the ability to provide highly efficient thermal transfer in a reduced footprint, meaning that capital costs are minimised while operating efficiency is increased.
No matter what process you are carrying out, checking it against the DOWNTIME acronym will prove to be a useful business exercise, but it is also important to use the same thinking when designing or specifying any new processing equipment. Good machinery design which adheres to these principles will make the subsequent management of DOWNTIME much easier, when the facility is fully operational.