In the fast-paced world of warehouse operations, the rise of goods-to-person picking (GTP) systems has brought about a significant transformation. This efficient order fulfilment technique utilises automated storage and retrieval systems (ASRS) to transport items directly to the operator at a workstation, revolutionizing traditional manual warehouse operations.
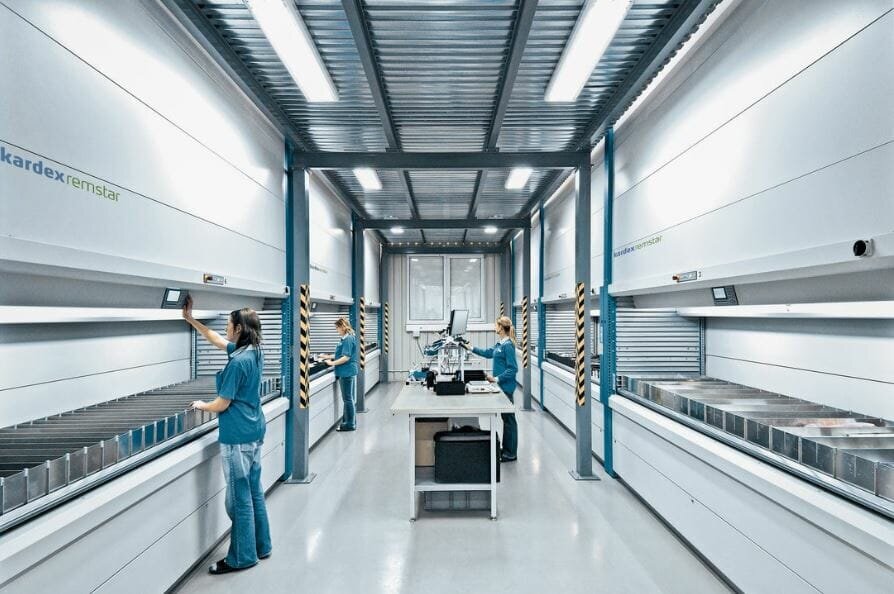
Unlike the traditional method of manual picking, which requires workers to navigate through aisles to gather items, GTP brings the goods to the person. By eliminating the physical strain of navigating the warehouse, GTP enhances worker ergonomics and boosts productivity. The operator can now efficiently fulfil orders with ease as the goods are delivered directly to their workstation.
The prevalence of goods-to-person picking systems has skyrocketed as the demands placed on warehouses continue to grow. These systems have proven to be a game-changer, improving both efficiency and effectiveness. By eliminating the time wasted on walking between different locations, operators can remain in their designated work areas, making better use of their time and reducing labour costs.
Furthermore, the benefits of GTP extend beyond productivity gains. Employers often face substantial indirect costs when workers sustain on-the-job injuries, with expenses that can be two to twenty times higher than the direct costs involved. Even seemingly minor incidents can accumulate and contribute to these costs. Implementing GTP systems not only enhances warehouse safety but also reduces the risk of injuries, thereby mitigating the hidden expenses associated with worker injuries.
Today’s goods-to-person picking systems are equipped with advanced technology, such as pick-to-light displays, which precisely indicate the location and quantity of items required for accurate picking. This feature significantly reduces the time spent searching for specific items. Furthermore, picks are intelligently sequenced within the ASRS, optimising the machine’s movement to provide items to the operator in the most efficient order. This maximises picking efficiency by enabling all items to be picked in a single rotation or cycle of the storage bins or trays.
Companies that implement automated goods-to-person picking systems often find that they can maintain their current labour levels while enjoying increased productivity. The improved picking capabilities enable the consolidation of multiple picking operations, meeting the rising demands of orders and accommodating the addition of more items to the inventory. Alternatively, implementing such solutions allows facilities to reduce labour requirements and overcome labour scarcity challenges in certain areas.
To enhance employee performance and minimize workplace injuries, organizations are increasingly adopting goods-to-person picking systems for warehouse order fulfilment tasks. Conventional warehouses often see workers spending a substantial amount of their time walking through shelving aisles in search of stored items. By eliminating unproductive and physically demanding travel and search time, automated goods-to-person picking systems enhance warehouse safety and contribute to a more efficient workflow.
ASRS technologies are designed with ergonomic delivery in mind, creating a work environment that prioritises injury prevention. Consequently, the implementation of such systems leads to a reduction in absenteeism, lower insurance premiums, and fewer claims for workers’ compensation.
In the ever-evolving landscape of warehouse operations, goods-to-person picking has emerged as a transformative solution. By revolutionising order fulfilment techniques and prioritising worker safety, GTP systems offer a promising future for warehouses and distribution centers worldwide
Want to learn more click here