There are two main options for gas analysis in industrial processes or emissions; the analyser can be located inside the gas stream (in-situ), or a sample can be removed from the gas stream (extractive) and transferred to an external gas analyser.
As a gas analyser developer and manufacturer with a history that dates back to 1977, Signal Group predominantly focuses on extractive analysers, and in the following article, the company’s Managing Director, James Clements, explains why.
Firstly, it is important to be clear that that one method is not necessarily better than another, because the choice depends on the application. Where is monitoring required? which parameter(s) are necessary? how quickly should data be provided? what are the process conditions? etc.
Proponents of in-situ analysers might claim that extractive analysers present higher risks due to the perceived potential for condensation in the sample line. Gases could dissolve in this moisture and go unmeasured, they say, and moisture could conceivably run into the analyser causing damage to metallic components. The manufacturers of extractive gas analysers and sampling systems are obviously aware of this, so monitoring systems are designed to prevent it from happening. For example, sample lines and measurement cells are heated to remove any possibility of condensation, and only non-corrodible materials are allowed to come into contact with a sample.
In-situ analysers are also exposed to risks; mainly because sensors are directly exposed to untreated, hot and potentially corrosive process gas. In addition, in-situ systems may be exposed to vibration which could cause misalignment of optical components, and/or the measurement point may be within a classified hazardous area, which would complicate design and installation work.
If the monitoring requirement is for a single parameter in a ‘clean’ gas flow within an industrial process for which real-time data is used for process control; in-situ analysers are likely to be ideal. This is mainly because in-situ analysers can be lower in cost, and would be capable of delivering faster results. Nevertheless, there are many other (probably the majority of) applications in which an extractive analyser would be preferable, and this is the reason why Signal Group has focused on developing extractive gas analysers for the last 45 years.
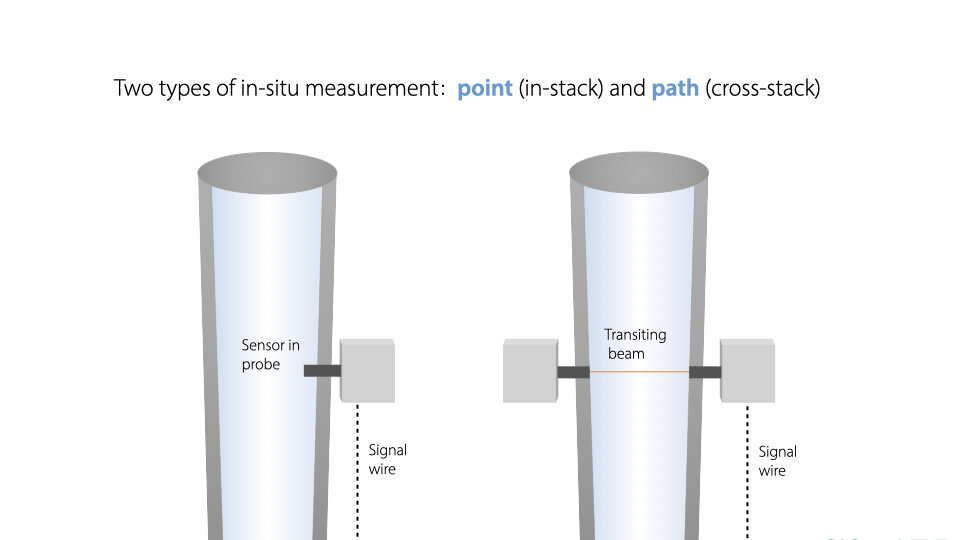
Multiple sampling points
An in-situ analyser might be suitable where only one measurement point is required, but another measurement point doubles that cost; a third trebles, and so on. In contrast, an extractive analyser can be multiplexed – connected to a multipoint sampling system so that one gas analyser can take measurements from multiple points in the same line or from different lines, to dramatically lower the cost per measurement location.
Convenience and Health & Safety
Anyone involved with gas monitoring will tell you that the ideal measurement point is rarely easy to access. Typically, it will either be located deep within a processing plant, in a confined space, alongside hot equipment, or it will be high up on a stack and exposed to all forms of extreme weather. A major advantage of extractive gas analysers therefore, is that they can be located in a convenient location, so that access for the purposes of maintenance or calibration, is simple and safe.
Calibration
Notwithstanding the safety and convenience considerations mentioned above, extractive gas analysers also offer advantages in calibration because they only require very small amounts of calibration gas. Operators of in-situ monitors would need to flood the stack or duct with calibration gas at the normal stack temperature, or rely on the instrument’s built-in calibration cells.
Maintenance
In-situ analysers can either contain a measurement cell within a probe that is inserted into the stack or gas stream, or they may use a cross-stack optical method. Both of these methods risk contamination that may affect accuracy, or in the case of optical instruments prevent measurement completely when the instrument’s windows become obscured by particulates or other materials.
Cross-stack instruments send an optical signal such as a laser across the duct or stack and reflect the signal back to a detector. Alternatively, the detector may be located directly across from the signal generator. Alignment is therefore crucially important, and frequent maintenance may be necessary if the instrument’s windows are obscured. The advantage of extractive analysers therefore, is that the sample can be filtered and conditioned to prevent contamination from affecting the readings.
Flexibility
The range of measurement technologies that are suitable for in-situ measurements is limited in comparison with extractive techniques. For example, Signal Group’s extractive analysers include options such as FID, CLD, NDIR, PMG and TDLS.
Extractive systems are also better able to accommodate changes in a process, waste stream or combustion material. So, an application that was originally better suited to in-situ might need to change to be extractive. For example, if it becomes necessary to measure new parameters; it is easier and generally less expensive to add that capability to an extractive system; largely because the sample handling system is already in place. Extractive monitors therefore help to future-proof monitoring capability. In summary, given the overwhelming number of advantages offered by extractive analysers in a wider variety of applications, it is hardly surprising that Signal Group continues to focus on extractive systems.