~ DC motors provide luxury while reducing aircraft fuel consumption ~
Despite being hit hard by the pandemic, the aviation industry is finally starting to recover — Bain & Company predict that by the end of 2022, global demand for flights will reach 84 per cent of 2019 levels. While customers expect more and more comfort features on their flight, the aviation industry must also address its emissions problem. Here Dave Walsha, sales manager at high performance brushless motor provider EMS, explores how electric motors can reduce aircraft fuel consumption while still providing luxury.
There is a growing trend of passengers looking for increased luxury and comfort on airplanes. In 2019 there were 21,979 active private jets registered around the world and industry predictions suggest this fleet will grow by 7,300 by 2030. Even on commercial flights, the introduction of premium economy — a halfway point between economy and business class — has made luxury travel more accessible to the masses.
Motorised comfort
There is a market trend toward using motorised features that provide comfort at the push of a button. On commercial planes these include motorised seat adjustment, which allows passengers to recline with ease. For most people, surfing the internet is an essential part of their day. An increasing number of passenger aircraft are equipped with communication antennas that continuously and automatically direct themselves to capture the best satellite signal.
In private and business jets, where there is virtually no financial limit on features and equipment, you can find even more futuristic comfort. Automation of many features, including window blinds, partition walls and armrests is becoming more common.
Keeping passengers safe
Electric motors also vital in a number of safety critical applications. There are many locking mechanisms on aeroplanes for cabin doors, emergency exits and the pilot’s seat, which must remain in a fixed position during take-off and landing. Motors are also used to adjust the valves that regulate pressure in the aircraft’s air-conditioning system.
Weight reduction
In 2019, the last year before air travel was affected by COVID-19, aviation emitted 918 million metric tonnes of carbon dioxide — an increase of 29 per cent on 2013 levels. The aviation industry must act now to reduce its emissions and play its part in the drive towards net zero.
Airlines are already taking action to reduce fuel consumption, in turn reducing the amount of greenhouse gases emitted, by cutting weight wherever they can — advanced materials, thinner seats, providing pilots with tablets instead of paper manuals and even giving passengers fewer ice cubes in their drinks.
Motors also play an important role. As motors are used for such a wide range of applications, their numbers on-board an aircraft are high. Using lightweight motors enables fuel consumption to be reduced, while still allowing passengers the touch of luxury they desire.
Electronic fuel injection
It’s not just commercial airlines that contribute to the emissions problem in the aviation industry. Currently, 15 per cent of carbon dioxide emissions come from non-passenger aircraft.
Unmanned aerial vehicles (UAVs) are smaller aircraft used as vital transport methods for the military, emergency services and, increasingly, industry for reconnaissance flights and measurement. To achieve extended flight time using minimal fuel quantities, these aircraft require reliable propulsion systems.
Smaller aircraft manufacturers are increasingly beginning to turn to electronic fuel injection (EFI) to provide the benefits of fuel injection to smaller aircraft. The system works by injecting fuel, which is under pressure in the system, into the intake manifold using special injectors and the fuel-to-air ratio is controlled using a control unit. Sensors in the intake and exhaust system of the engine feed data to an electronic control unit, where it is then assessed and the ideal amount of fuel required at a particular point is calculated. As a result, using an injection system can reduce fuel consumption by up to 30 per cent.
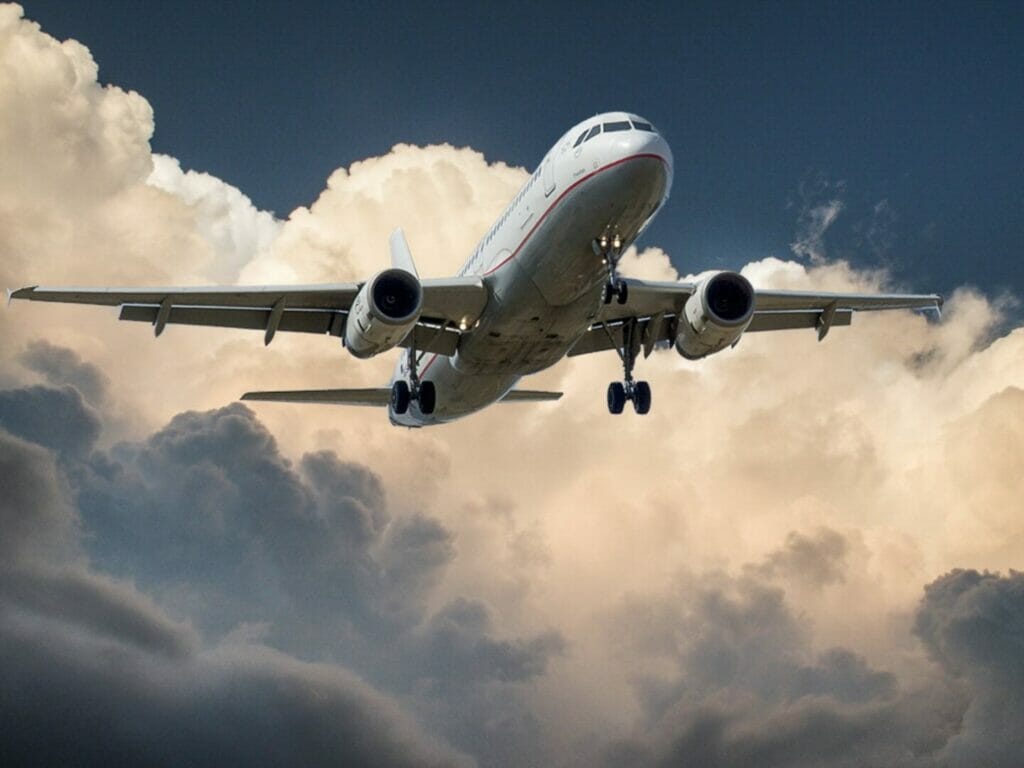
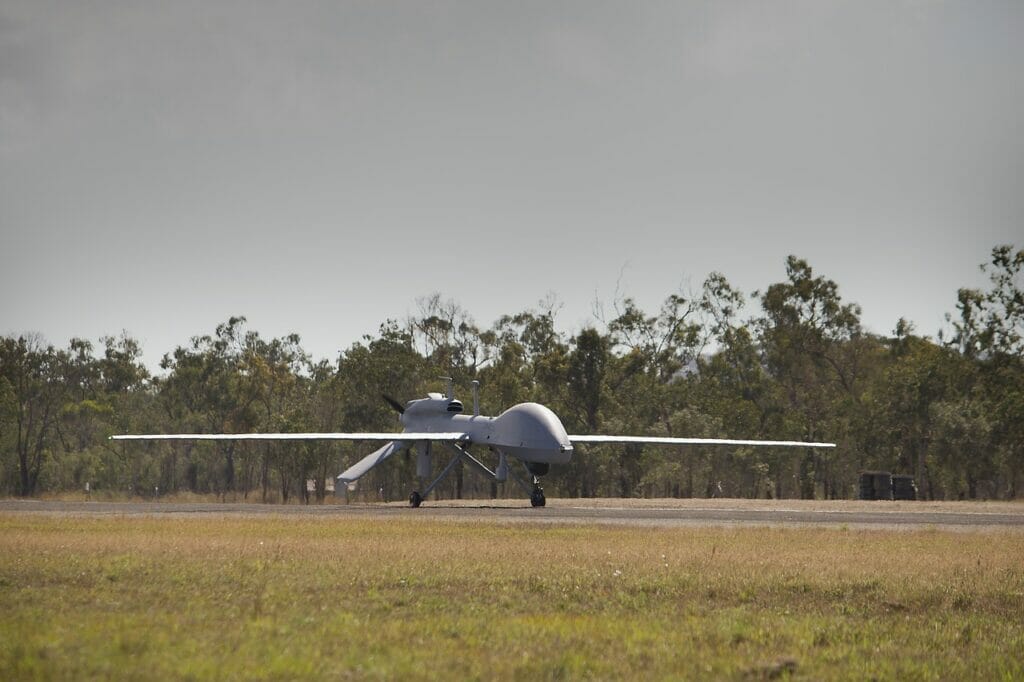
When designing an injection system for a small aircraft, everything needs to be minimised. The compact system consists of many components, including the injector, a fuel pump, ignition module and a fuel pressure accumulator. These mechanical components need to weigh as little as possible to keep the aircraft light.
A high-performance, low-weight small DC motor can fit compactly into an EFI system to help deliver consistent fuel pressure. The motor helps create the auxiliary energy required to build up the necessary pressure, which powers the fuel pump to deliver fuel and air into the system.
Reliable motors
In an EFI, motors must be able to work tirelessly, with low rotor of inertia for fast and reliable acceleration and braking. EMS is the sole UK supplier for FAULHABER motors, which are characterised by their high power and low weight. They can be incorporated as part of this fuel system without contributing to any unnecessary weight gain.
It is important that nothing fails or breaks during a flight, particularly where passenger and crew safety is concerned. Maintenance intervals should also be as long as possible. FAULHABER motors are made in a finely controlled manufacturing process that ensures consistent high quality.
As we take to the skies again, the aviation industry must work to keep its emissions under control. Reducing weight and improving the efficiency of fuel consumption is essential. Thanks to lightweight and reliable motors, it is possible to reduce emissions while still providing passengers with luxury and comfort as they travel.