~ Reducing rare earths consumption with reconditioned components ~
The Guardian recently announced that the deep-sea gold rush for rare metals has officially begun, with mining companies planning to profit from rare earths discovered 4,000 metres below the surface of the Pacific Ocean. However, with millions of tons of e-waste produced every year and increasingly sophisticated techniques to recover rare metals from it, a more environmentally-friendly alternative might be hiding in plain sight. Here Neil Ballinger, head of EMEA at automation parts supplier EU Automation, explains the role of reconditioned components in reducing our dependence on mining rare earths.
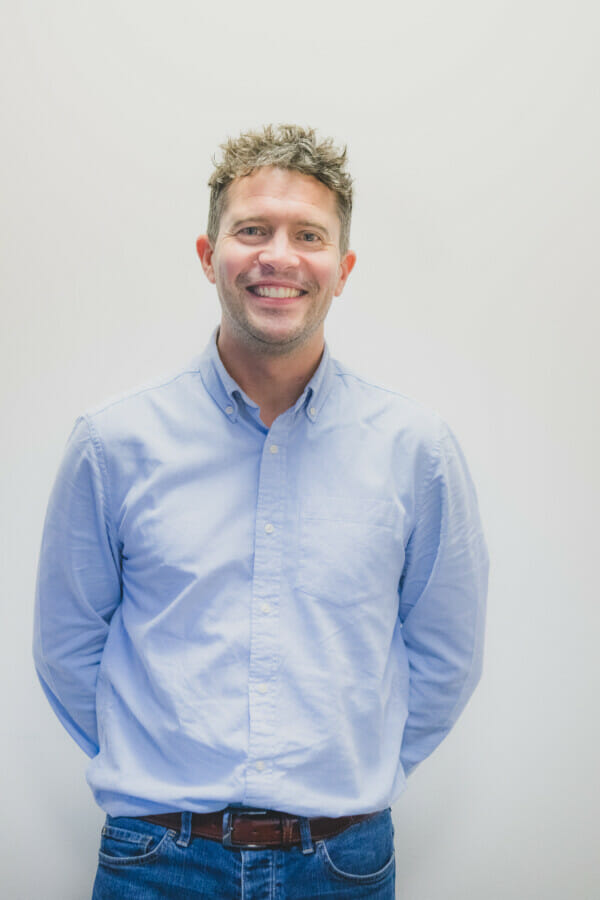
According to Statista, the global demand for rare earth oxides will grow from 208,250 metric tons in 2019 to an estimated 304,678 metric tons by 2025, an increase of 37.5 per cent. Rare earths are used in a huge variety of consumer technologies and high-tech devices, such as hard disk drives, as well as in clean energy technologies. For example, tantalum, the rarest stable metal, is widely used in wind turbines because of its unsurpassed energy storing capabilities.
Rare earths also find important applications in industrial automation. For example, servo motors rely on magnetic materials containing neodymium and dysprosium, while gallium is used in its liquid form in human-machine interfaces (HMIs).
Given their many applications, the demand for rare earths is rapidly moving beyond what our land can supply. As a result, mining companies are welcoming the possibility of exploiting deep-sea ore deposits, and hope that global guidelines to regulate extraction could be set in place as early as July 2023. However, environmental activists warn that this could have catastrophic consequences for delicate marine ecosystems.
Hiding in plain sight
While mining corporations look for the hidden treasure at the bottom of our oceans, an equally valuable one hides in plain sight.
In 2019, the global e-waste output was estimated to be 48.6 million tons, the equivalent of 350 cruise ships. With the COVID-19 pandemic triggering a massive surge in the use of digital technologies, we can only assume that this number is going to massively increase.
Many of our discarded devices, both consumer technology and industrial equipment, contain precious rare earths. Instead of rushing to mine rare metals from one of the few untouched ecosystems left on the planet, we should invest in viable methods of recovering the astonishing amount of these substances that are present in our discarded devices. At the moment, the process of retrieving rare earths from legacy technology, known as smelting, is very costly and energy-intensive, which is why more research is needed. So, what can we do as manufacturers?
Reducing our reliance on brand-new products is step one. For example, reconditioned or refurbished automation spare parts are a great alternative to new ones. These components have been cleaned, repaired and tested to perform as new, and come with a full warranty if purchased through a reputable source. On top of that, the current crisis of global supply chains means that refurbished products might have massively shorter lead times compared to new ones.
However, it’s important to distinguish between parts that have undergone a full reconditioning and testing process, and second-hand alternatives whose condition cannot be guaranteed. Sourcing from e-commerce sites such as Alibaba or eBay can be tempting, but the best solution is to rely on a trustworthy automation parts supplier who can provide full visibility into the part’s condition and the reconditioning process it has undergone.
Refurbished components are not only safe to use, they can also help the growth of a circular economy — the only viable model to reach the net-zero targets our planet desperately needs.
To order a wide variety of reconditioned automation parts from all major brands, visit www.euautomation.com.