In a space-saving product inspection breakthrough, Fortress Technology has custom-engineered a unique twin aperture metal detector and dual lane Raptor checkweigher for one of the world’s premium dairy companies, helping to halve waste.
Receiving shredded cheese pouches directly from a dual head bagger, the bold design unlocks substantial space and cost savings for the busy dairy plant.
Offering a customised solution that no other food inspection company could come close to in performance attributes, the twin lane conveyor configuration, consolidates a single Fortress metal detector uniquely divided into two apertures and two independent weight verification Raptor checkweighers for optimised quality control. Each technology and lane has its own air blast reject mechanism to isolate metal contaminants and weight rejects, helping to reduce and minimise good product being wasted by over 50 percent. Measuring just 10ft in length, Fortress also integrated a radius conveyor into the metal detector infeed.
For the producer of some of the world’s most iconic cheese brands, compromising on metal detection sensitivity was not an option. Highlighting the benefits of the multi-aperture metal detector concept European commercial manager Jodie Curry expands: “The high-spec Fortress multi-aperture system was engineered specifically to ensure that that there was no trade-off in terms of performance and metal detection sensitivity. One of the key benefits of a twin aperture system is the halving of waste caused by rejects.”
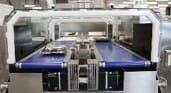
Multiple advantages
The special dual-lane version of Fortress Technology’s multi-aperture metal detector comprises a single unit split into two smaller dedicated apertures for each lane that act as independent metal detectors. For optimal metal detection sensitivity the two compact apertures – measuring just 102mm in height by 254mm wide – means that the packs pass individually right through the centre point of the metal detector.
“With output per hour being such a critical productivity benchmark, this game-changing multi-aperture design facilitates high speed and accurate metal detection and marks a step change for lean manufacturers seeking to reduce factory footprint and improve Total Cost of Ownership (TCO),” notes Jodie.
Fully integrated with the dairy plants’ upstream and downstream equipment and matching the 120-140 ppm output speed of the dual head VFFS bagging system, the compact geometry of the customised radius conveyor facilitates the positioning and orientation of product packs as they smoothly round the corner towards the metal detector. Providing optimal spacing between product packs as they are presented to each metal detector aperture helps to avoid congestion, bottlenecks and flexible packaging formats overlapping which could lead to sensitive weight verification checks being distorted.
As each lane is programmed to run independently, the bespoke design helps to minimise interruption to the packing process during product switchovers or if one lane stops working or requires maintenance. Additionally, the unique design gives the plant extra inspection and weight verification capacity, as two different product lines, pack sizes or SKUs can be run simultaneously adjacent to each other.
Air blast nozzles located between the two outfeed conveyors efficiently and independently remove contaminated product into lockable reject bins equipped with reject confirmation and bin full sensors. With heavier products, Fortress would typically suggest using a pusher, drop conveyor or retracting belt mechanism.
A Rapturous reception
Using compatible collective parts, the inaugural integration of the new Raptor Checkweigher marks another big milestone for the inspection specialist. Delivering dynamic weight monitoring with minimal customisations to existing product feed and packing lines, the hygienic dual lane design also targets operational inefficiencies, notably upstream product giveaway, non-conforming food packs and packaging waste.
In just milliseconds two packs pass over two Raptor load cells to weigh, analyse, capture and report data simultaneously. For ease of integration, air blast nozzles reject out of weight specification products with minimal operative intervention.
To ensure absolute traceability and compliance with retailer Codes of Practice and QA protocols, both the metal detector and Raptor checkweigher capture easy to read live OEE data. Enabling the dairy group to establish the operational parameters and extract statistics most valuable to their business, for instance volume, weight, inspection speed, rejects or downtime.
Equipped with Contact Reporter software, the dairy plant has the facility to export and convert time-stamped production data. “This level of cohesive reporting on a multi-lane system provides valuable upstream trend feedback to boost operational efficiencies,” notes Jodie.
Constructed to the highest food grade standards, the modular 200mm wide conveyor assembly, conveyor decks and belts are all designed to be easily removed from the machine for rapid deep sanitation and maintenance. Operatives simply unclip and disconnect the conveyor motor. In just seconds, the conveyor belt is removed, and the belt tension and tracking is instantly restored when clipped back into place. All without using a single tool.
In 2021, the Fortress Raptor series won the prestigious Food Processing Lean Manufacturing accolade. Commending the natural synergy between metal detection and weight verification technology, judges hailed the high operational efficiency, cost savings and utilisation of common elements.