No moulded part is too big or too small for Omega Plastics. Especially given the company’s recent installation of a new precision IntElect 50-ton machine from Sumitomo (SHI) Demag. Supplied with two interchangeable barrels and screws, the quick-change system gives Omega Plastics the flexibility to produce micro-structured components with a shot weight of less than 0.1g up to 22g, supporting the surge in UK OEMs seeking to nearshore and procure plastic parts from trusted local suppliers.
Pre-pandemic Omega Plastics was already observing an unprecedented shift among OEMs towards single-contract domestic sourcing. Winning multiple new opportunities in the automotive, medical device, optics and electronic fields, the new all-electric addition has enabled the Northeast of England moulder to upscale its Micro Injection Moulding (MIM) offering.
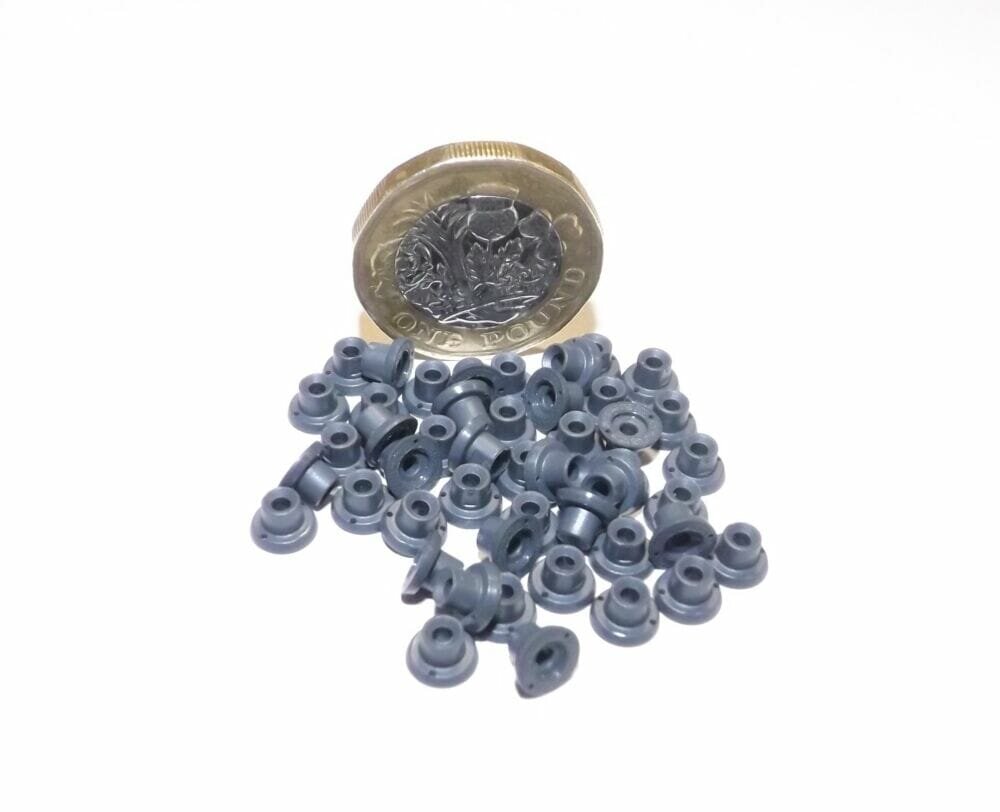
For a high-quality turnkey supplier like Omega Plastics, moving into the MIM space is a natural transition. Investing in another IntElect machine – its third across the company’s two production sites – supports this wider micro precision moulding expansion strategy.
Despite the reduction in component sizes, the company astutely opted for a larger IntElect 50-ton machine with generous 360mm square tie bar and mould space for added production flexibility and to accommodate complex mould designs. The injection unit’s direct drive guarantees a more stable and repeatable process. Sumitomo (SHI) Demag spokesperson Ashlee Gough explains: “This level of precision is only attainable with all-electric ‘direct drive’ technology. Conventional hydraulic machines typically struggle to manage fluid compressibility, which can have a detrimental effect on the consistency of the screw stroke.”
Optimised screw geometry
Ordinarily, a 50-ton machine would be used to run all sorts of components with shot weights much larger than 0.1g. Having the option to rapidly swap between a 14mm screw and cylinder for micro parts and a 22mm option for larger precision and multi-cavity components, boosts production capacity for Omega. It also ensures that dosing is optimised to each application.
Ashlee Gough continues: “The 14mm screw is the smallest capable of processing standard thermoplastic pellets for shot weights of 0.1g up to 9g. It facilitates the small shot weights and fine control required for MIM and enables users to manufacture components with dimensional accuracy requirements of a micron or less.” Conversely, the 22mm screw geometry can be used with a higher number of cavities to handle shot weights of between 3g and 22g.
Overall efficiency, machine uptime, fast cycle times and quick interchangeable barrels were all influential factors during Omega’s selection process. Compared with competitor micro moulding systems, the IntElect won hands down in the timed barrel change trials. Five newly trained operatives at the 24-hour production site continue to challenge themselves to beat their 45-minute best.
Julian Jamieson, Group Operations Director noted: “The machine is a great fit for our varying demands, particular the ease at which you can change the barrel to suit shot size requirements, reducing downtime and improving OEE.”