Several thousand health and safety workplace incidents and cases of ill-health within engineering environments are reported to the Health and Safety Executive (HSE) every year.
The cost of these incidents can be disproportionately high within the engineering industry as the loss of workers through injury or ill-health is likely to disrupt production and company profitability.
The majority of reported accidents and cases of ill-health within engineering are a consequence of movement in and around workshops; be it people, vehicles or goods.
Of these accidents about half involve slips, trips and falls with the remainder resulting from lifting or moving goods, machinery or equipment.
HSE provides specific information and guidance (HSG129) for people who run and work in engineering environments; such as workshops that make products and those that repair plant machinery.
The risks that are likely to be of most concern in these workplaces include those associated with manual handling, the use of machinery, noise, vibrations, and hazardous substances.
Other ‘non-movement’ accidents within engineering typically arise from the use of machinery, including electrical accidents and occupational diseases such as deafness, asthma and mobility problems.
This article looks in more detail at some of the health and safety risks within the engineering industry and how they can be mitigated using the correct safety and security solutions.
Moving around the workplace
It’s already been highlighted that about two thirds of all accidents in engineering workshops occur during the movement of vehicles, people and goods.
A safe, well-lit, clean workplace can help prevent many of these.
The Workplace (Health and Safety and Welfare) Regulations 1992 and Approved Code of Practice outline what employers must have in place to ensure safe movement around the workplace.
This includes:
- Safe access for pedestrians and vehicles – separate access points and passages may be required.
- Level, slip-free surfaces
- Handrails installed where necessary i.e. on stairs or ramps
Site safety specialists, such as SafeSite Facilities, can supply a range of safety barriers and cones that may be used to create safe passage ways, entrances and exits for those on foot and for vehicles.
Two of the most flexible safety barrier choices are gate barriers and centipede barriers. Gate barriers are highly reflective providing increased visibility around hazardous areas. They can easily be integrated with other types of barrier systems via a ‘hook and eye’ connection, and they have in-built anti-trip feet for added stability and safety. Centipede barriers are a cost effective, retractable safety solution available in two heights (1.2m or 1.8m) which expand to a maximum length of 2100mm. When retracted they measure 400mm, meaning they are easy to transport and store. Featuring lockable, rubber wheels, centipede barriers can be used indoors or outdoors without damaging floors.
Column/pillar protectors are another consideration to cushion the blow of any impact on internal or external posts or supports. Other measures that may be used to improve health and safety practices internally include impact protection systems (such as cross-bars and railings), as well as cable and hose ramps, to allow vehicles to pass over cabling safely, and to limit trips and falls.
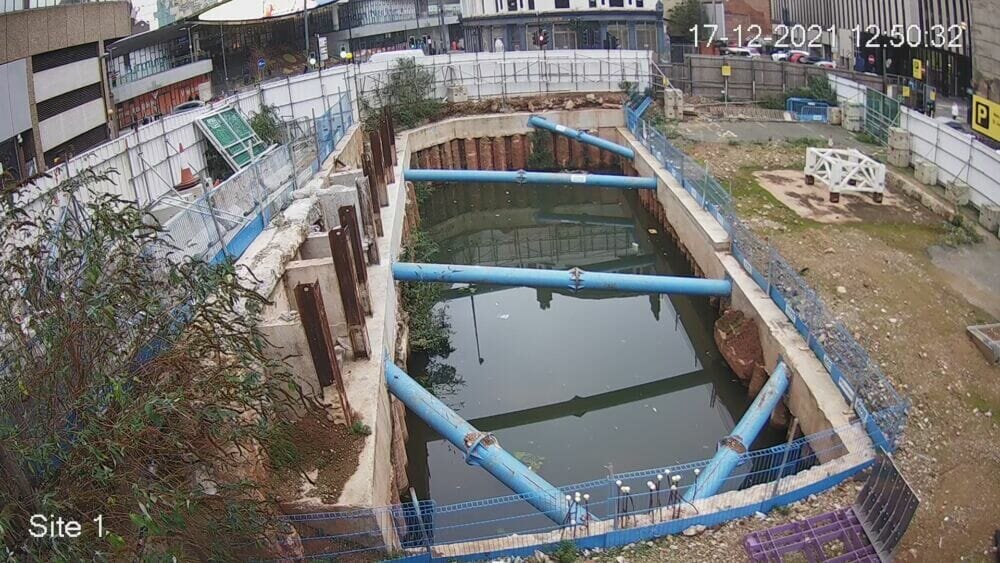
Uneven and wet surfaces can lead to slips and trips. Ground protection provides a temporary or permanent solution even in the most challenging weather or surface conditions.
The COVID-19 pandemic has shone a spotlight on hand hygiene, to help reduce the risk of infection transmission. Portable sanitisation stations, located throughout the workplace, encourages staff and visitors to observe regular hand hygiene measures for their own safety and that of others.
The benefits of Closed Circuit Television (CCTV) for health and safety purposes is two-fold. CCTV provides a watchful eye on potential hazards, and, in the event of a health and safety incident, will also capture crucial evidence of the accident. The site pictured here shows CCTV monitoring in action to watch over a water-storage area. There are detection lines set around it so if anyone breaches the secure area, it alerts the monitoring station.
Other safety considerations
The use of hazardous substances is a common within engineering environments and workshops. Welding, metal-working, and degreasing involves dangerous solvents, liquids and fumes. Prolonged exposure to chemicals can cause headaches, skin irritation and other short and long terms side effects. Particular care must be taken when using and storing hazardous substances and areas where they are used must be kept clean and well-ventilated at all times.
Exposure to noise, for example through the use of power and punch presses and other machinery is another important health and safety consideration. Machinery can also cause high levels of vibration which should also be managed. Steps must be taken to reduce noise and vibration, for those involved in these engineering processes as well as the workforce around them. HSE inspectors have previously reported that the noisiest item may sometimes even be a radio! HSE provides a useful breakdown of typical noise levels for a variety of engineering processes and how to reduce them.
HSE is currently reviewing its guidance to help manage risk within the engineering industry. Updated content will be published on its website in the coming months. In the meantime HSE’s Instant Action Checklist is a useful tool to start a risk assessment and review and action workplace conditions without delay.