The interest in and adoption of automation and robotics within the UK’s food and beverage sector has grown significantly in recent times, driven by several different factors. As a sector which in the past had access to a large pool of manual labour, which could be recruited and deployed as required, will the growth of automation and robotics continue as we have seen in the last year, or will manufacturers once again seek to return to a reliance on manual labour to meet future demands?
There is no doubt that the combined effects of the Pandemic, Brexit and general overall uncertainty in recent times have been the catalyst for some UK food and beverage manufacturers to turn to automation as a solution to their resource and productivity issues.
According to statistics from the International Federation of Robotics, the UK’s food and beverage industry almost doubled its installations of robots from 155 units in 2019 to 304 units in 2020 (+96%,) an unprecedented rise in a single year. These new robots and automation systems have been introduced across a number of different processing, packaging, and handling operations.
The availability of robots suitable for use in High Care environments has opened up a range of new applications says CME’s Ian Marks Head of Sales – Automation. “One of the areas hardest hit during the Pandemic were the meat processing facilities where normally large numbers of operators would work in close proximity to each other. In addition, the COVID-19 virus seemed to thrive in these low temperature environments. Automation in these areas brings a host of benefits, aside from the obvious boosts in efficiency and performance. Automation and robots are not sensitive to these low temperature environments and will operate uninterrupted 24 hours per day. In addition, even with the tight restrictions on operator hygiene and cleanliness, and the use of PPE, there is still a risk of product contamination. Automation, on the other hand can be designed to meet even the strictest criteria within the food and beverage sector whilst continuing to operate at the highest efficiency levels.”
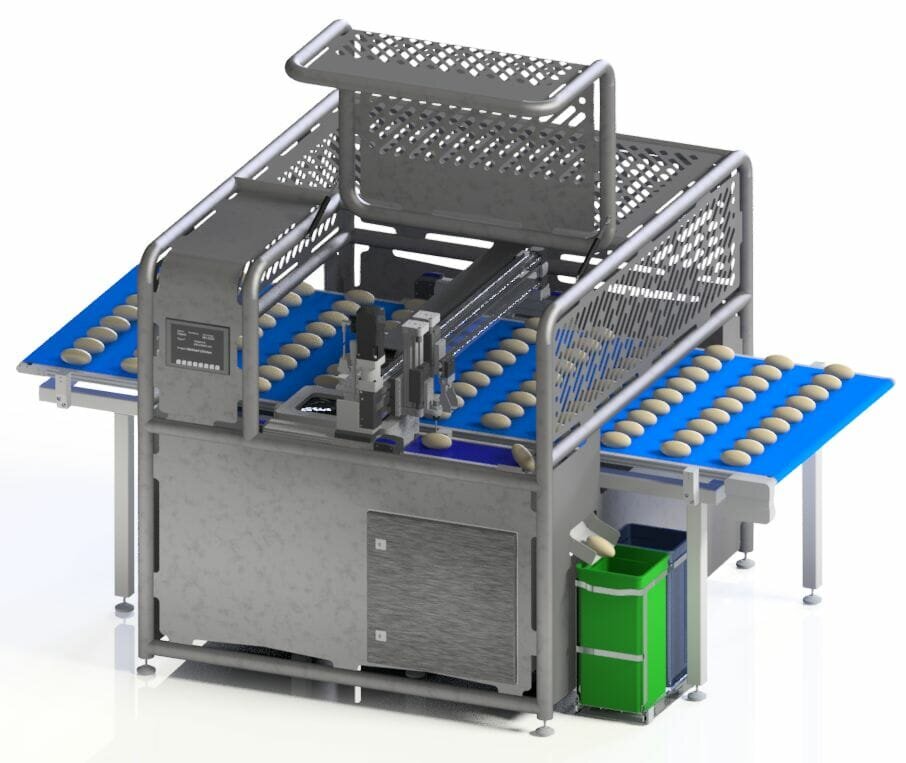
(The UK’s Food & Beverage Sector can benefit greatly from the introduction of automation in its many forms”)
Whilst some of the most obvious targets for automation are applications where product is to be picked, handled and packed, there are potentially numerous other opportunities for manufacturers to introduce automation to improve consistency, quality and productivity. CME’s Ian Marks continues: “One example where the introduction of automation can deliver significant process improvements, minimise the need for manual input whilst eliminating risk for operators is through the introduction of an Automated Core Temperature Probe System.”
The traditional method for checking and recording the core temperature of food products during production is entirely manual. An operator is required to remove a product from the line, manually insert a temperature probe and wait for a pre-determined time before recording the temperature by hand. Any deviation by the operator from the required checking interval or defined procedure can result in not only inaccurate information but potentially serious health risks for the consumer.
The introduction of an automated solution here not only mitigates the ongoing difficulty in recruiting, training, and retaining manual operators but also eliminates the requirement for operators to calibrate and use their manual temperature probes correctly. The automated solution also means that operators are not reaching into a hot environment to select product for testing. One of the biggest benefits is an increase in productivity due to reduced waste.
CME’s Ian Marks explains “By taking control of the process through the use of automation, products can be removed from the line at pre-determined and selectable intervals, and from all areas of the line to evaluate any cross-band temperature variation. The automated process uses machine vision to ensure that the temperature probe will be inserted in the right position on the product. The probe will also be inserted to the correct depth and for the correct time to provide accurate and reliable data, which can be used to monitor any trends in temperature variation and for traceability purposes. Product which has been tested can either be returned to the line or segregated as required.”
The introduction of automation makes it possible for companies to enhance the role of their existing operators. Training and upskilling operators to operate, manage and maintain automated solutions alleviates the boredom often associated with mundane repetitive manual tasks. Also, at a time when many individuals have taken a step back and looked closely at their work / life balance, their careers and the potential for more interesting roles, manufacturers who introduce automation and robotics can use that opportunity to foster greater loyalty amongst employees who can see the potential for progression.
There is now a great opportunity for the UK’s food and beverage sectors to build upon the positive steps taken in the last year or so and to fully embrace the potential which automation and robotics holds. Of course, investment is required, but aside from the financial payback which business seek, automation delivers predictable performance and output which is not at the mercy of fluctuating availability of a manual workforce.
To find out more about automation opportunities within your business contact CME on [email protected]