Fully automatic picking of unknown products from bulk material
In intralogistics, there has been a real hype about robotics for some years now, whether in trade journals or at fairs. Most of them are classic six-axis articulated robots that are looking for their way out of a production environment and into logistics. The goal: fully automated small parts picking. The main driver here is the labour shortage, the big challenge not a technical component like the robot or the gripper, but the design of an overall economic process. Since robots can only handle a portion of the items in each assortment, there are parallel streams of goods and thus possible risks with regard to the flow of goods, inventories, synchronisation and consolidation.
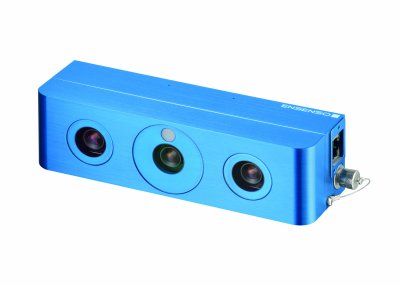
The “autopick” picking robot from psb intralogistics GmbH in Pirmasens (Germany) meets this challenge. At its core, the fully automated solution for picking individual items consists of a robot with gripper, the IT network for the entire system and a powerful image processing system – equipped with two Ensenso 3D cameras from IDS Imaging Development Systems GmbH.
Application
The vision system acts as the eye of the robot. It detects grippable surfaces on the objects to be processed in the source container and calculates grasping points and collision-free paths for the robot. This enables the robot to pick up unknown products directly from bulk material and place them in the target bin in the area with the lowest filling. Vacuum cups ensure gentle gripping of the respective objects. A previous “teach-in” of the individual products is not necessary. Regardless of whether it’s a medicine bottle or a tea pack, the multifunctional gripper can be individually designed for a wide variety of articles with the most diverse packaging units. The system learns over time which of the different graps works best for each item. The achievable picking performance for a process-safe system is highly dependent on the characteristics of the gripping objects and ranges between 300 and 500 parts per hour.
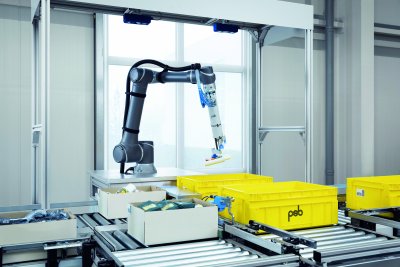
The robot picks up unknown products from bulk material and places them in the target container – 300-500 parts/h depending on the gripping object
Two Ensenso N35 3D cameras provide the system with the necessary image data. All Ensenso 3D cameras work according to the “Projected Texture Stereo Vision” method. Each model uses two CMOS sensors and a projector that projects high-contrast structures onto the object to be captured – even in difficult lighting conditions. Ensenso cameras operate using stereo vision, which imitates the human vision. The result is a 3D point cloud as the basis for the required spatial object information.
To integrate the cameras into autopick, psb intralogistics used the Ensenso SDK. In addition to wizards for easy setup and to support camera calibration of the 3D cameras, it includes the option for GPU-based image processing for even faster 3D data processing.
It also enables the output of a single 3D point cloud of all cameras used in multi-camera operation, which is required in this case, as well as the live composition of the 3D point clouds from multiple viewing directions.
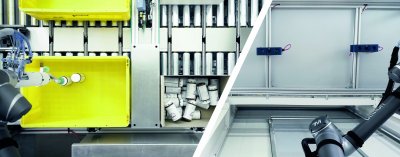
Two Ensenso 3D cameras provide the system with the essential image data
The first camera is installed above the source box in order to consider the latter as a collision object in the path planning of the robot arm. Here the unknown parts are presented and the point cloud for searching the appropriate handle point is generated. The latter is done with the help of the Mikado ARC (Adaptive Robot Control) software from isys vision. It combines Ensenso’s 3D stereo vision camera technology with an easily configurable, adaptive robot controller. The result is a complete 3D robot vision solution for bin picking and parts handling with an autonomously operating robot, as supplied by autopick. Instead of following predefined, taught and firmly defined paths, it orients itself independently in the workspace and reacts to every situation.
The second camera is above the target box. It searches for free storage positions. In addition, the Z-height of the box content is determined in order to be able to take this into account when determining the storage position. It is crucial that the target box is occupied evenly and that the products are placed carefully. The latter is particularly important when picking fragile parts. The image acquisition is asynchronous to the movement of the robot in order to optimise the cycle time.
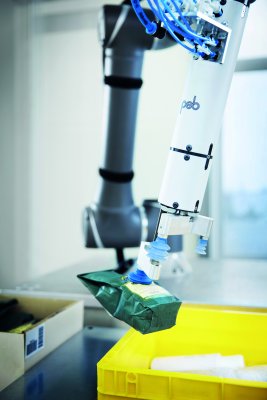
Multifunctional vacuum cups ensure gentle gripping of a wide variety of items
“We chose the Ensenso N35 for its compact design and high point cloud quality. For the considered field of view, the N series is ideal. The configuration of the camera can be easily and precisely adjusted to the respective product portfolio, or even adapted during the process,” explains the system manager at psb intralogistics. Handle information and picking orders are exchanged via the interface to the warehouse management system.
Outlook
Online trade continues to have strong growth ahead of it. At the same time, the e-commerce sector is becoming increasingly tough. Innovative intralogistics technologies are therefore often necessary to remain competitive. At the same time, hardly any economic sector is currently struggling as much with the lack of suitable young talent as logistics. The economic benefit of picking robots is therefore so substantial that they will have a permanent place in commissioning in the medium to long term. The underlying solutions with artificial intelligence will learn to master other challenges besides gripping – independently or also collaboratively in cooperation with humans, reliably and precisely. Image processing with 3D cameras, among others, provides the decisive overview and the necessary safety.
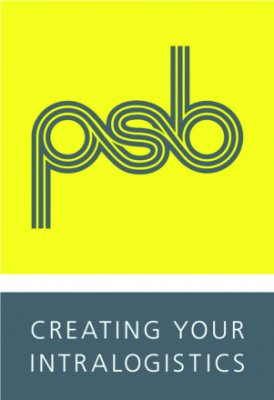