The Sinzig based mechanical engineering company FEDDEM GmbH & Co. KG is pleased to be able to provide an overview of its LFT pultrusion lines for the production of long glass fibre pellets as well as on the subject of upcycling and service in addition to its FED 43 MTS extruder at Fakuma 2021.
FEDDEM will be presenting a twin-screw extruder of the type FED 43 MTS 32 L/D in Hall A6/6217. With a screw diameter of 43 mm and up to 142 kW drive power, this extruder size is ideal for pilot and production applications of small to medium batch sizes.
The FED 43 MTS model range offers all the typical FEDDEM advantages that are of great benefit in compounding and masterbatch applications:
- Highly efficient melting and mixing of product components through the use of FME mixing elements. Kneading-block-free screw geometries prove their worth in a wide range of applications.
- Modular, thermally insulated protective covers of the processing section as protection against contact and for a more favourable energy balance of the process.
- Process length can be individually adapted by extension unit
- FSB side feed(s), FSV side vacuum deaeration, FSE side vent(s) each with quick connections (mechanical, electrical and, if applicable, for cooling water connections).
- FSK strand head, compact and equipped with swivel hinge. On request, also available with patented arched nozzle for special applications.
- Robust design of all system components for continuous operation.
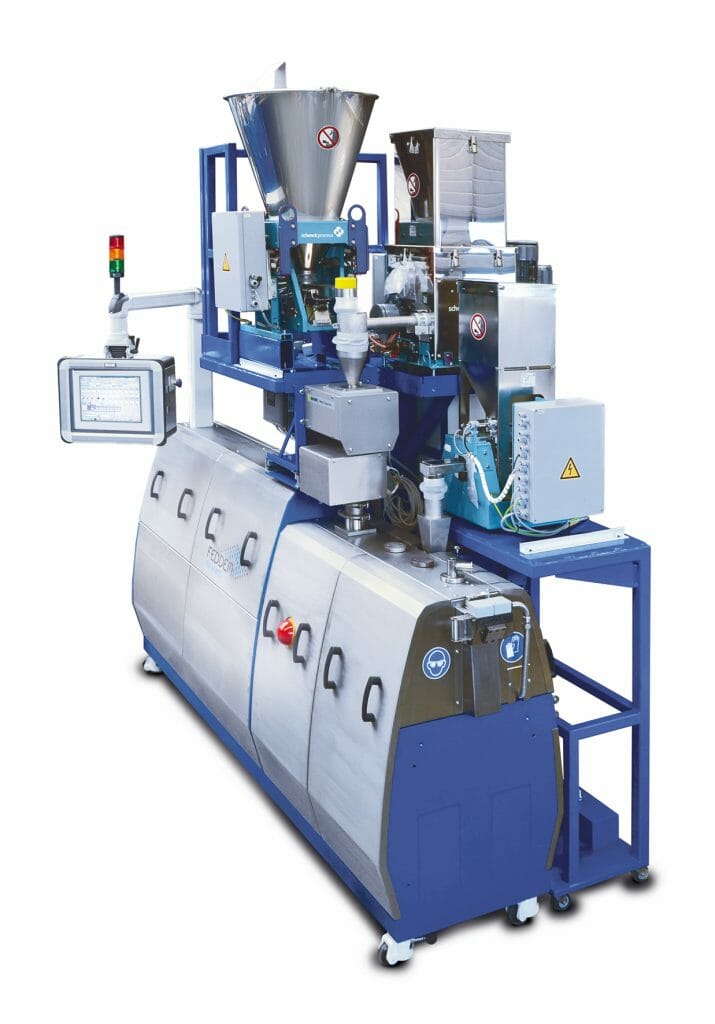
FED 26 MTS extruder with 3 gravimetrically metered material streams and metal separator in the main stream.
Practical optimisation of LFT pultrusion line technology for the production of high-performance materials
“The technology of LFT pultrusion lines for the production of LFT-G long pellets has been around for several years. FEDDEM has taken a fresh look at the details of the line components to improve performance, quality and handling. The result is not only unprecedentedly tight tolerances from the fibre content in the pellets, but also the repeatability of the achievable material properties of the LFT compound on different lines and line sizes with haul-off speeds of up to 60 m/min,” says Klaus Hojer, Business Development Manager at FEDDEM GmbH & Co. KG.
This was made possible, among other things, with a patented, modular impregnation tool. The extruder for melt preparation is installed parallel to the roving line, which allows considerable savings in the space required by the plant. All maintenance access points for the individual plant components have been designed to allow direct and fast access to ensure the highest possible plant availability.
Upcycling
In order to keep as much plastic as possible in production in the course of global efforts, compact plants for the processing of production waste are becoming increasingly interesting. In upcycling applications, twin-screw extruders are proving their worth in terms of high mixing performance in a gentle process that delivers high-quality recyclate. Additives can be incorporated into the process that, for example, adjust the viscosity and colour of the recyclate for optimal reuse.
At the same time, the space requirement can usually be reduced to a minimum, which can be a great advantage when setting up in the production environment (see Fig. 1).
“Screw geometries for FEDDEM extruders in these applications are equipped with FME mixing elements for gentle processing. The processing section can be equipped with a variety of wear protection types, depending on the application” says Hojer.
To overcome investment hurdles, the company also arranges attractive leasing solutions for smaller systems.
Service
In addition to its plant technology, FEDDEM also offers a wide range of services. From measuring process parts to assessing the overall condition of a plant with recommendations for maintenance measures.
“In the meantime, augmented reality (AR) has found its way into everyday service – even to the point of remote commissioning of a plant on another continent,” Klaus Hojer reports.
The company will be happy to provide visitors to the fair with detailed information on this topic.