By acquiring Vischer & Bolli Automation, the German manufacturer of high-precision workpiece clamping equipment has not only expanded its expertise in the field of automation, but now offers an even wider range of stationary workpiece clamping devices. The zero-point clamping system for a quick change-over with a 5-axis clamping.
Hainbuch’s previous product portfolio for turning, milling, EDM and grinding already covered a wide range of workpieces. Now, since the acquisition, the Hainbuch Group is able to offer custom solutions for workpieces of up to 100 tons or 10 to 20 metres in length, large-scale projects like this have already been completed. Thanks to Vischer & Bolli Automation, the range of stationary devices has been considerably extended. Many stationary clamping devices are available from stock and the modular design of the zero-point clamping system offer a wide range of solutions using standard components, while specific solutions can also be created in accordance with customer requirements.
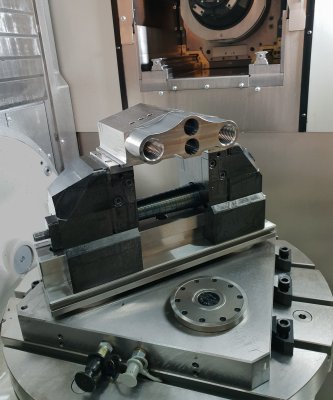
Total solution: zero-point clamping system serves as the base
The zero-point clamping system, which is screwed onto the machine table, serves as a base for fast change-overs. This is available in pneumatic and hydraulic versions and is used for manual and automated solutions. To clamp the workpiece on the base, a vice [mechanical, pneumatic or hydraulic], clamping tower, modular clamping device, modular clamping system, magnetic clamping plate or a special device can be used depending on the customer´s requirements. This means that an optimal and economic overall solution can be offered for every workpiece, regardless of shape or size. The zero-point clamping system has an accurate clamp and thus ensures maximum back force. At the same time, it is absolutely low-wear and maintenance, as it has only three moving parts. Handling and push-off functions are integrated in the system. The modular design ensures maximum flexibility and huge time and cost savings in production. With the universal interface, the setup is done off the machine so no production time is lost.
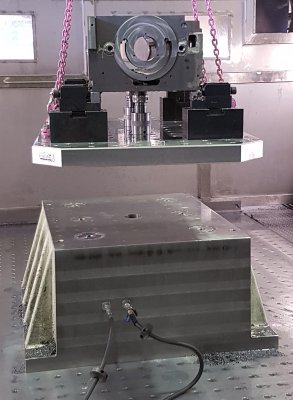
Zero-point clamping system console with K5000 modular clamping device during the change-over process.
Standardized locking plates and mounting cylinders for the zero-point clamping system
The patented collet style lock ensures easy insertion and removal of the workpiece pallets. With an insertion force of up to 30 KN, a vibration-free, positive and non-positive connection between the zero-point clamping system and the workpiece is guaranteed. Tailor-made custom solutions help to make optimum use of machining potential. Direct installation on machine tables, pallets or fixtures is achieved cost-effectively with installation cassettes. The zero-point clamping system can be expanded with optional air blow, support and locking control or external feeds.
Advantages of the zero-point clamping system:
– Setup in parallel with production – reduces machine downtime by up to 90 percent
– Work can be interrupted at any time – maximum flexibility for urgent jobs
– Zero-point repeatability < 5 µm
– Cost-effective clamping bolts – simple retrofitting of existing clamping devices
– Better surface quality due to dynamic, vibration-inhibiting as well as positive and non-positive clamping
– Suitable for automation
– Designed for more than 1 million clamping cycles