Small wastewater treatment works (WwTWs) frequently present significant physical challenges for instrumentation and control engineers. However, a compliant flow measurement facility has been installed at a plant in Fowey, in the south-west of England, by a partnership involving a water company, a contractor, an instrumentation provider and an inspection company.
The flow monitor at Fowey WwTW needed to be replaced as part of a capital maintenance programme which was challenging due to the constrained nature of the site. Therefore, more innovative solutions were considered as an alternative to a like-for-like replacement.
Engineers from Tecker, a MEICA contractor for South West Water, therefore reviewed the available options. “The channel is in-between two aeration ditches, and there was insufficient room to extend or divert the channel,” explains Tecker Project Engineer Ben Finney. “We therefore considered repairing or replacing the flume, but an alternative suggestion was made that we contact Nivus to see if their cross-correlation flow meter might be able to deliver accurate flow measurements without the costs and problems associated with capital works.”
Background
Accurate wastewater flow measurement enables the managers of treatment plants to operate efficiently – optimising treatment, minimising costs and protecting the environment. Consequently, through MCERTS, the Environment Agency places strict performance requirements on flow monitoring devices and structures at WwTWs in England. The MCERTS performance standard establishes the minimum requirements for the self-monitoring of flow.
The MCERTS standard applies where a site has a permit under the Environmental Permitting Regulations (EPR) requiring the process operator to monitor liquid flow of sewage or trade effluent, and to collect and record the results. MCERTS specifies the minimum requirements for self-monitoring of flow where operators have installed meters to conform to the Environment Agency’s permit requirements. Natural Resources Wales permits may also specify that flow monitoring systems are certified against MCERTS.
Regulated flow measurement systems and structures are usually inspected annually, and non-compliance can be triggered by a number of factors such as ageing and eroded channels, or a failure to deliver the requisite levels of accuracy due to changing flow volumes. For example, growth in the local population combined with increasing rainfall intensity due to climate change, can result in flow structures ‘drowning out’.
Flow monitoring at Fowey WwTW
Following Tecker’s request, engineers from Nivus visited the site and specified the instrumentation requirements, based on the Nivus NF750 transmitter, a cross-correlation velocity sensor combined with ultrasonic level measurement. “The popularity of this technology has grown enormously in recent years,” says Rob Rhyder from Nivus. “This is frequently because the flow meter can be quickly and easily retro-fitted to damaged or ageing channels, without having to implement significant capital works.”
Explaining the advantages of this solution, Ben Finney says: “The cross-correlation flow meter was delivered within a month of the order and installation took less than a week. In contrast, work to repair or replace the flume would have taken much longer to organise and implement; it would have cost a great deal more; normal operations of the plant would have been impacted, and there would have been no guarantee of MCERTS compliance. We were therefore delighted that the Nivus solution was implemented so quickly, and that it passed the MCERTS inspection.”
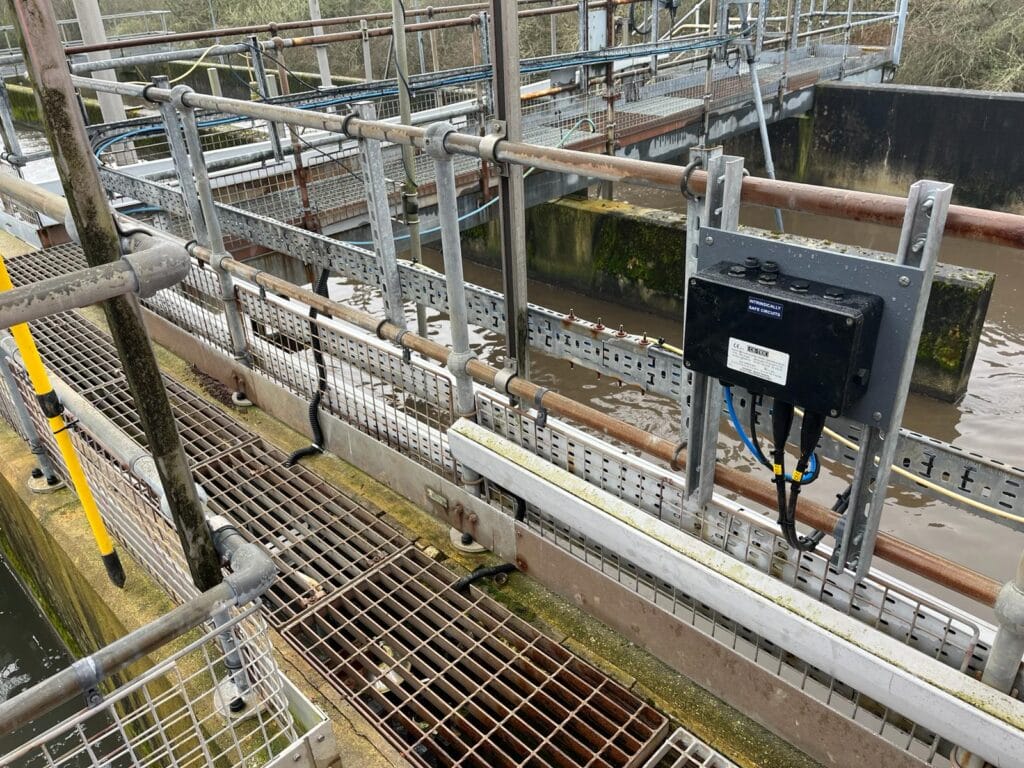
Cross-correlation flow measurement
Nivus has developed a unique ultrasonic cross-correlation method, in which individual velocities are measured continuously at different levels within the flow section. This area velocity flow measurement technique provides a 3-dimensional flow profile that is calculated in real-time to provide reproducible and verifiable flow readings.
The flow velocity measurement method is based on the principle of ultrasonic reflection. Reflectors such as particles, minerals or gas bubbles within the wastewater are scanned using an ultrasonic impulse with a defined angle. The resulting echoes are saved as images or echo patterns, and a second scan is conducted a few milliseconds later. The resulting echo patterns are saved, and by correlating/comparing the saved signals, the positions of unambiguously identifiable reflectors can be identified. The reflectors can be identified at varying positions within the images since they have moved with the water.
By utilising the beam angle it is possible to compute the particle velocity and hence the wastewater flow velocity from the temporal shift of the reflectors. This technology produces highly accurate readings without the need to perform additional calibration measurements.
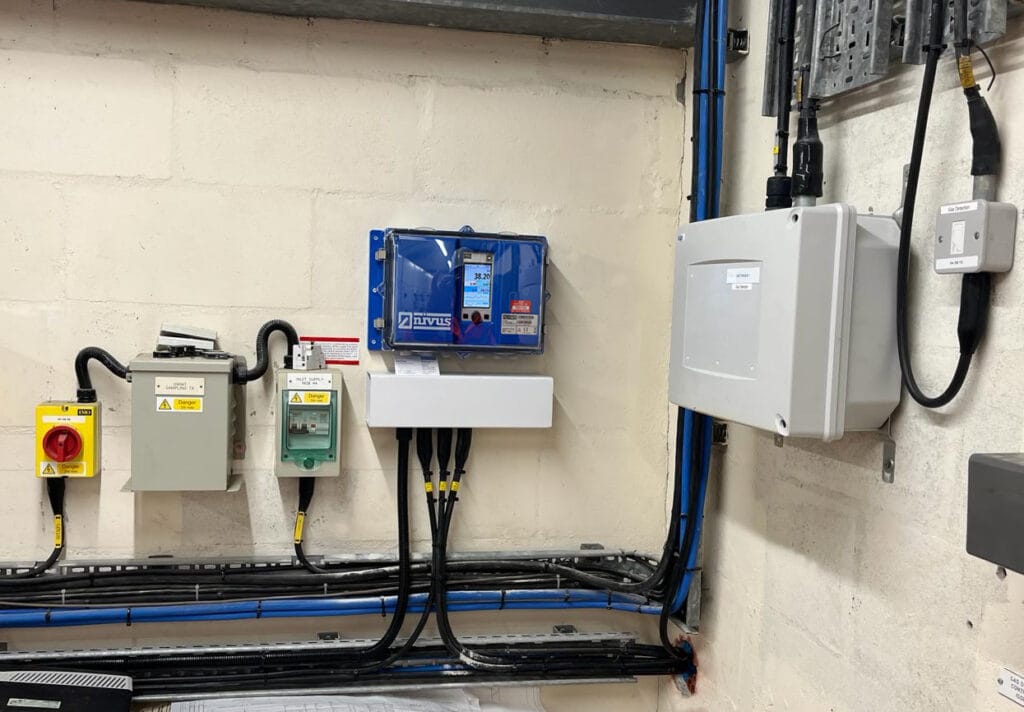
Designed for operation in channels or pipes, the technology is able to operate effectively in the most demanding, heavily polluted applications. Influencing factors such as flume shape, discharge behaviour and wall roughness are all accommodated within the flow computation.
The Nivus cross-correlation technology is able to conduct flow velocity measurements in levels as low as 3 cm, with additional velocity sensors (maximum 9) deployed in larger flows, measuring flow velocity in up to 4 metres of depth. As a consequence of this flexibility, the technology is applicable to a wide variety of flow structures.
The inlet channel at Fowey is 300mm wide so just a single wedge sensor was required, and Nivus provided bespoke bracketry so that it could be deployed quickly under any process conditions.
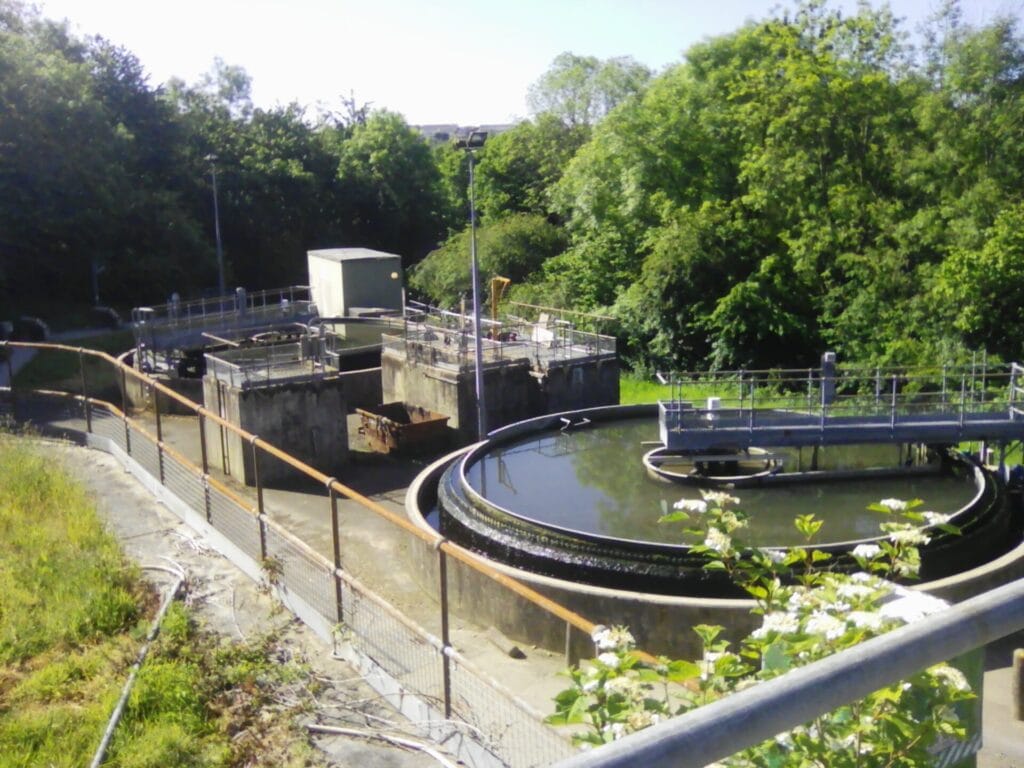
Summary
Following the installation of the Nivus NF750 transmitter, the flow measurement facility was tested and passed MCERTS, without any impacts on the plant’s treatment processes. Looking forward, Ben Finney says: “It is likely that we will utilise area velocity flow meters in more applications because they are sufficiently flexible to be able to accommodate a wide variety of hydraulic systems. In addition to the reduced costs and faster installation times, one of the most important advantages is the minimised requirements for process impact.” Emphasising the importance of a partnership approach, Ben adds: “Obviously, we were keen to ensure that the flow installation received MCERTS approval, so it was highly beneficial to accommodate the views of all stakeholders from the beginning, including the MCERTS inspector.”
Dave Curtis, South West Water MEICA Specialist, said: “More demanding requirements from the regulator combined with challenging process scenarios mean that the need to consider alternative technologies is essential. The Nivus technology has been recognised by South West Water for some time and features on approved equipment lists. The technique offers a valuable tool in our armoury where the application does not suit other closed pipe or noncontact methods.”
Leave a Reply
You must be logged in to post a comment.