Jochen Kern, Head of Sales & Marketing, micrometal
The Photo-Chemical Etching (PCE) processes utilised by the micrometal Etching Group have significantly revolutionised the production of precision metal parts, providing innovative solutions that were once deemed impractical or impossible. This article explains the different etching processes available, and explores how micrometal’s uniquely precise reel-to-reel PCE process has been effectively implemented in the production of coffee filters for an Italian company renowned for its high-quality coffee machines.
OVERVIEW OF PCE TECHNOLOGY
The standard sheet PCE process, developed to create intricate and precise metal components, stands out for its ability to produce parts with very fine detail and high accuracy. Put simply, the process involves covering a metal sheet with a photo-resist mask that is then exposed to UV light to imprint a design. The unexposed areas of the metal are subsequently etched away with chemicals, resulting in highly precise components with smooth finishes and complex geometries. This technique is especially beneficial for producing parts that are difficult to manufacture through traditional machining or stamping due to their delicate nature or complex designs.
The micrometal Group provides an optimised traditional sheet PCE process, but has also developed a uniquely refined reel-to-reel PCE process which is used in the manufacture of the coffee filters.
In the area of precision engineering, micrometal Group’s reel-to-reel PCE process represents a significant advancement, enabling the meticulous fabrication of metal parts with complex geometries on a scale suitable for mass production. The technique incorporates a sophisticated liquid resist system to deposit remarkably thin photoresist layers 2-8 microns thick. This innovation is crucial as it substantially increases the precision of the etching process, allowing for the creation of features on metal as diminutive as 25 microns, with the accuracy of dimensions held within a few microns.
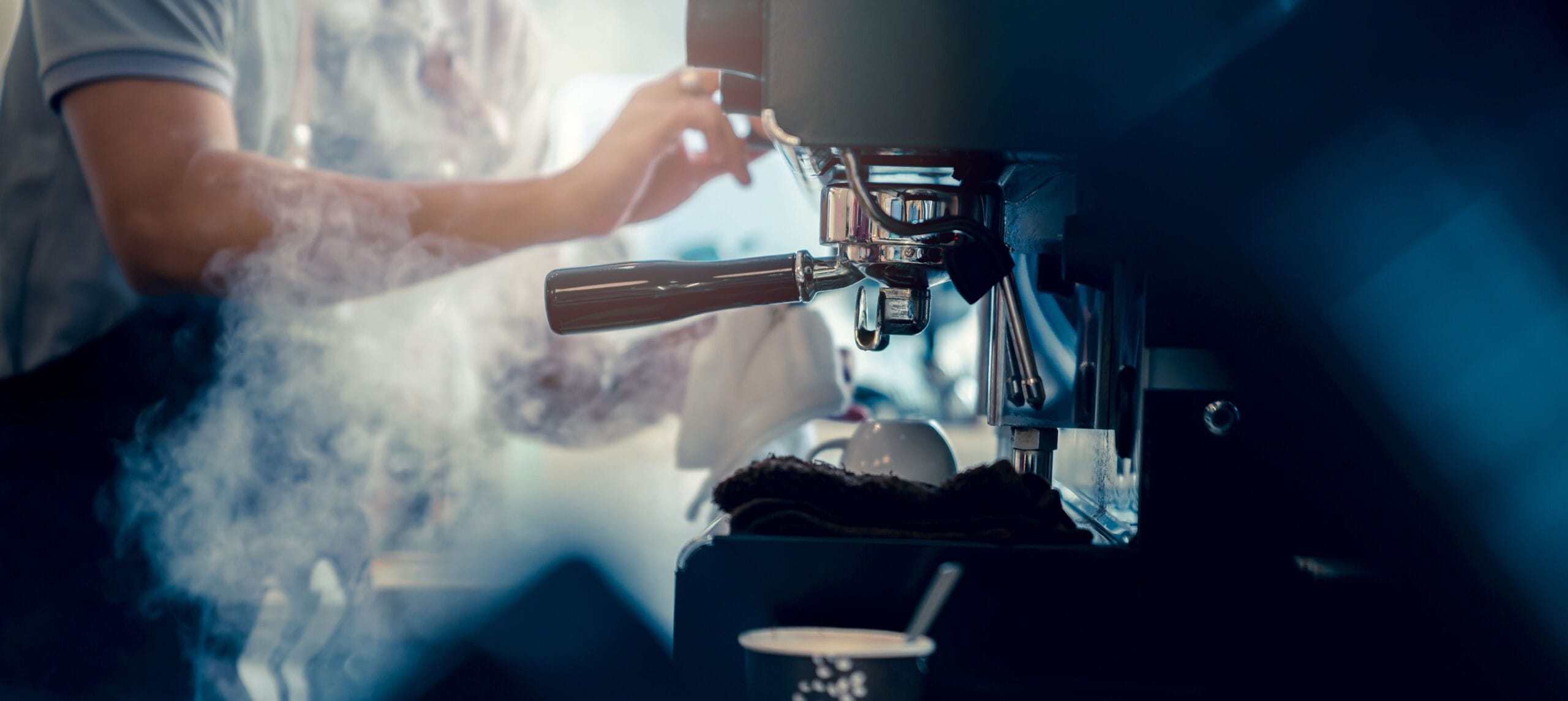
micrometal Group also utilises glass tooling in its reel-to-reel PCE process allowing the manufacture of intricate and precise metal components like coffee filters. Glass tooling has the advantage of being highly durable and resistant to environmental factors like humidity, which can cause distortion in film tooling. This leads to achieving tighter tolerances in the range of 1-2 microns. Moreover, the glass tooling does not wear out over time and does not impart stress on the metal being processed, ensuring the parts remain flat and free from deformation.
The operational sequence of the reel-to-reel etching process is a study in control and precision. It begins with the metal strip unwinding from a reel, traversing through a sequence of chemical treatments and light exposure, and culminating with it being rewound onto another reel as the processed etched product. Control over this process is imperative. Factors such as the temperature, the chemical concentration, and the agitation of the etchant must be regulated precisely to guarantee that the final product maintains uniformity and precision. The technology allows for the handling of metal strips varying in thickness from 25 to 400 microns, with the capability of producing continuous metal strips that can extend up to 800 meters.
Upholding the integrity of the production process, the micrometal Group adheres to a rigorous quality protocol, continuously refining and supervising each stage of the etching cycle with advanced metrological instruments. Such a comprehensive focus on quality control ensures that the etched components align with the stringent specifications demanded by discerning sectors such as aerospace, medical technology, and electronics.
This level of precision is not just about meeting standards but also about pushing the boundaries of what can be achieved with metal component fabrication.
COFFEE FILTER SIEVES
High-resolution sieves used in the consumer industry require precision in the micron range and mass production needs to be cost-effective. micrometal Group’s reel-to-reel PCE process meets both these challenges, and as an example of its usefulness and agility, its use by an Italian Company which makes coffee machines using highly precise coffee filters is a perfect example.
Coffee filter sieves must be able to withstand high stresses caused by pressure in the coffee making process or cleaning. This requires that the sieves are made of high-strength stainless steel for a long service life. Hole geometry is also important, and through the use of PCE, it is possible to etch holes that are strongly funnel-shaped (conical), meaning the narrow opening of the holes on the filtration side do not have any depressions, stopping solid particles getting stuck in the holes.
Hole sizes and tolerances are optimally matched to the size and size distribution of the coffee powder. For brewed coffee, a small ratio of hole size to average coffee grain diameter
(> 65 μm) is used to avoid undesirable powder residues in the coffee. For optimal crema and fine sediment in espresso, a slightly larger ratio is chosen. A filter of approximately 100 mm diameter designed for this application contains up to 420,000 conically shaped micro-holes.
For such an application, photo templates are created on the basis of a technical customer drawing and the given product specifications. The metal material to be etched is unwound from the strip, cleaned and coated on both sides with a light- sensitive liquid resist layer. Then a glass tool with the negative image is placed on both sides of the coated tape and directly contacted by applying a vacuum. Subsequently, the etching template is exposed. The coated and exposed metal is developed and the unexposed areas on the tape surface are removed.
Combining suitable photo templates with the specific unique characteristics of the etching process allow a wide variety of breakthrough shapes and surface textures to be created when making sieves and filters. Obvious pan-industrial applications in addition to coffee filtration include filters and screens, coding discs, catalytic converter foils for the automotive industry; lead frames, RF shielding, and connectors for the electronics sector; springs, vapour deposition masks, shaving foils, fuel cells, diffusers for various industrial applications; needles, implants, and microfluidics for medical application; and decorative etching products and jewellery.
CONCLUSION
The adoption of PCE for a range of industry applications, exemplified by its use in coffee filter production, underscores its transformative impact on manufacturing processes. micrometal’s uniquely precise and versatile reel-to-reel PCE process not only meets the high precision and durability requirements of modern manufacturing but also promotes cost-effectiveness and efficiency in mass production settings. This technology continues to stimulate innovation, offering a competitive edge to industries that integrate it into their production lines, thereby reshaping traditional manufacturing paradigms.